Abstract
With the widespread use of downhole pressure gauges (DHPGs) to measure and record downhole pressures in oil and gas wells, engineers have been able to eliminate/reduce the wellbore effects that can mask true reservoir response. However, not every well is equipped with a downhole gauge; even fewer have the downhole gauge at the mid-completion depth, leaving fluids below the gauge that are subject to frictional pressure drop and changing fluid density/head due to heating/cooling. The reservoir signal (delta pressure vs. time) can be slightly masked or completely overwhelmed by the change in pressure head due to changing fluid density as the well bore fluids cool or heat up. The resultant measured rate of pressure change will, therefore, not be representative of the actual reservoir response. In addition, frictional pressure loss as fluids travel up the well bore can appear as pressure loss due to completion skin. This causes wells to have an artificially high skin. using raw pressure data that has not been accurately corrected for changing fluid head/density and frictional losses below the gauge can lead to inaccurate pressure-transient analysis (PTA) results (Hasan 199).
This paper will discuss the physics of these processes and explain the reasons for these errors in the PTA results, along with the impact of these errors. Finally, a method for properly correcting the measured pressure to mid-completion pressure will be described. To demonstrate the effects, case studies conducted on two gas wells, a gas-condensate well, and an oil well will be presented.
Introduction
Pressure gauges are no longer an expensive commodity, compared to the cost to drill and completing a well. High resolution, accurate, repeatable and thermally compensated gauges are relatively inexpensive and abundantly available in the form of Quartz based or Piezo-electric based gauges etc. In general, the ability of a modern gauge to measure, record and correct pressure data is of decreasing concern, assuming that the data is not being excessively filtered and is being recorded and stored at a sufficient frequency. However, it is up to the analyst to correct the data for wellbore effects to ensure accuracy in PTA results. In other words, the pressure transient analyst is decreasingly restricted by the gauge’s performance, and mainly restricted by the ability to process the data to calculate a representative reservoir pressure response.
While it is well-known that the failure to account for friction below the gauge results in an artificially high skin, there is little recognition that the phase and thermal transient behavior has a significant impact on the permeability calculation. When both of these effects are neglected, wells may be unnecessarily stimulated, or have errors in calculating the reservoir permeability and in-place volumes. The wellbore modeling method presented in this paper significantly reduces/corrects these artificial errors in PTA calculations.
Background
To truly understand phase and thermal transient behavior in a well bore, it is imperative to take a closer look at the path produced fluids take to reach surface and it is also important to consider the surroundings and the heat transfer that occurs within the well bore and between the well bore and the surroundings.
We can classify wells as onshore and offshore wells – offshore wells can be further classified into dry tree and wet tree. The temperature profile inside and outside the well bore behaves differently depending on whether the well is shut-in or flowing, in addition to the historic production of the well and the time in the current flow rate and composition. Any changes in rate will affect the temperatures in the well bore as a function of the heat load from the reservoir fluids and the loss of heat to the surrounding pipe, cement, rock, water and air. This is most noticeable when a well is flowing or shut-in. These temperature changes also affect the phase behavior of the fluids in a well bore at various points along the well. It is important to mention here that temperature and pressure are inputs to calculating the bottomhole pressure (or pressure at any point in the well bore). Therefore, an accurate wellbore model that accounts for change in wellbore temperature over time is needed. In some cases, the change in temperature (and fluid density) is so drastic that the pressure response and the subsequent pressure transient analysis results are meaningless unless the temperature change is accounted for in the bottomhole pressure conversion (Fair, 2002).
Temperature gradient inside well under static conditions (shut-in)
When the well is shut-in it loses heat to the surrounding formations by conduction. Since the wellbore fluids are coldest at the top and hottest at the bottom, axial transfer of heat by natural convection occurs as well. In an offshore well, the section of the well bore that is adjacent to sea water is conduction dominant and forced convection may occur depending on the velocity of the currents. The section of the well bore exposed to air will have relatively less heat loss due to conduction per given length as compared to the section in sea water because the thermal conductivity of air is much lower than that of water. In this part of the paper the assumption is that the well has been shut-in for a long time and that the wellbore fluids have reached thermal equilibrium with the surroundings. Hoang (1980) demonstrated that wellbore fluid temperature gradients are within 4 percent of the geothermal gradients within 3 days of shut-in. This is a good rule of thumb for onshore wells; however, offshore wells (especially dry tree deepwater wells) may not reach thermal equilibrium for weeks.
Fig. 01 depicts a temperature profile of an onshore well under static conditions, i.e. after a long shut-in. The temperature between the top of the X-mas tree until the tree-rock interface is the same as the atmospheric temperature. The tree-rock interface is an effective pivot point for the temperature profile. Below the ground, the temperature profile follows the geothermal gradient.
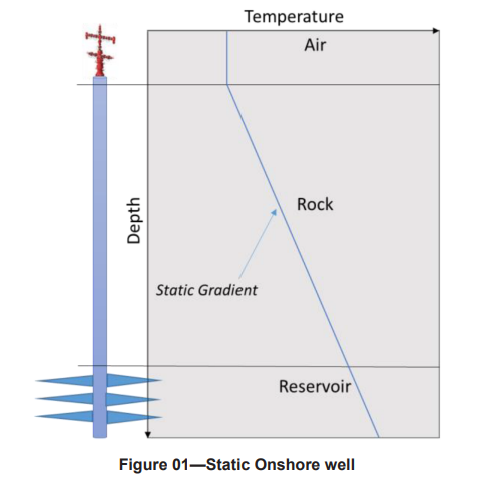
Offshore wells can be categorized as dry-tree and wet-tree wells. In wet-tree (subsea) wells, the X-mas tree is located on the sea floor. The first few feet below the sea floor comprise of a partially compacted muddy substance before the transition to rock begins. For convenience this region will be referred to as “mud”. The temperature in this region is influenced by the seawater, but is increasingly influenced by the geothermal gradient as the depth increases. The “mud” has a relatively higher overall heat capacity due to the presence of free water when compared to the more consolidated formations below it. Therefore, it is slower to respond to temperature changes (both warming and cooling). Once the “mud” ends and rock begins (this distinction is based on the static temperature with depth), the geothermal gradient prevails. In other words, the mud-rock interface is another pivot point for the temperature profile. Fig. 02 depicts a schematic for a dry-tree well, the top of the wellhead is surrounded by air and the temperature of the fluids in this region is the same as the temperature of the atmospheric air. Below the air-water interface (pivot point), the well is surrounded by water and the temperature of fluids inside the well bore would be the same as that of the seawater (if the well has been shut-in for a sufficiently long time). Note that depending on the geographic location of the well and the depth of the water, the water can be warmer or cooler than ambient air conditions. The figure showing the thermal profile of an offshore well (Fig. 02) is for a scenario where the water is deep enough to cool with depth and where the ambient temperature is higher than the seafloor temperature (note that this is not always the case in cold climates). Below the water-mud interface the well is surrounded by mud. Below the mud-rock interface (pivot point) the well is surrounded by rock, the temperature of which is determined by the geothermal gradient – temperature generally increases in a near-linear fashion with depth. The air-water, water-mud and mud-rock interfaces act as pivot points. If there are unusual hot spots, cold spots or active aquifers in the rock, thermo-clines in the water, or other deviations from a representative response along any of the sections of the pipe/well exist, additional pivots can be added. It should be noted that these descriptions are not universal and that a static pressure/temperature survey needs to be performed to determine the effective static profile for the well. These measurements can often be extended from one well to other wells in a field
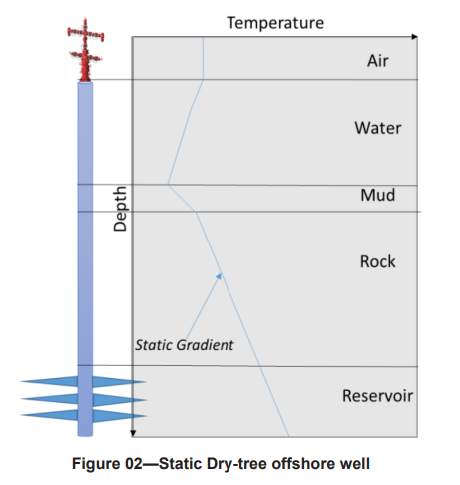
Temperature gradient inside the well under dynamic conditions (flowing)
When a well starts to flow the nature of the heat transfer is more complex due to moving fluids as compared to the heat transfer in a shut-in well. The reservoir acts like a heat source – fluids from the reservoir travel up the well bore transporting heat and a thermal transient is initiated. The temperature gradient in the well bore becomes dominated by the heat load from the reservoir and the heat sink of the formation/mud/water/air and changes at every point in the well bore, parametrically. The higher the flow rate (fluid velocity), the lesstime it takes for a molecule to travel up the well bore and the lower its temperature decrease. Therefore (and in general), the higher the rate, the higher the temperature at any point along the well bore. Note: For start-ups of dry tree deepwater wells, the wellhead temperature (WHT) can actually decrease due to the displacement of cooler fluids in the well near sea floor depth where the water temperature is the coldest and effects of conduction and forced convection are both in play. Similar logic can apply to ambient air temperature being warmer or cooler than the well fluids. However, the use of pivots and proper initial conditions can correct for these effects.
Unless the well is at a thermally static equilibrim (and ignoring the potential start-up effects of seawater, mud and ambient temperature), the wellbore fluids will have a higher temperature than the surrounding strata/fluids. Due to the higher temperature inside the well bore at any given depth, a temperature gradient now exists between the well bore and the surroundings (tubing, annulus, casing, cement, formation, water, air, etc.). Heat is transferred to the surroundings mainly via conduction and since the heat source is effectively infinite, it could take anywhere from a few hours to a few weeks for temperature to reach equilibrium in this region at a given flow rate and wellbore composition. Assuming that the steady-state heat flow from the fluid to the wellbore/formation interface equals the heat flow from the interface to the formation and also assuming that inside the earth there is no heat diffusion in the vertical direction, one can expect one-dimensional radial diffusion (Pourafshary 2007). The temperature near the well varies radially away from the well and is also time-dependent. Heat loss from the wellbore fluids decreases with time (Kabir 2002). After a certain distance away from the well, the formation temperature follows the geothermal gradient. Thermal diffusivity determines and defines how heat is transferred in the radial direction to the surrounding porous media. The new flowing temperature profile is more curved, as opposed to linear (for the static thermal gradient). Fig. 03 and Fig. 04 illustrate the new temperature gradients in flowing wells after the temperature reaches steady-state conditions.
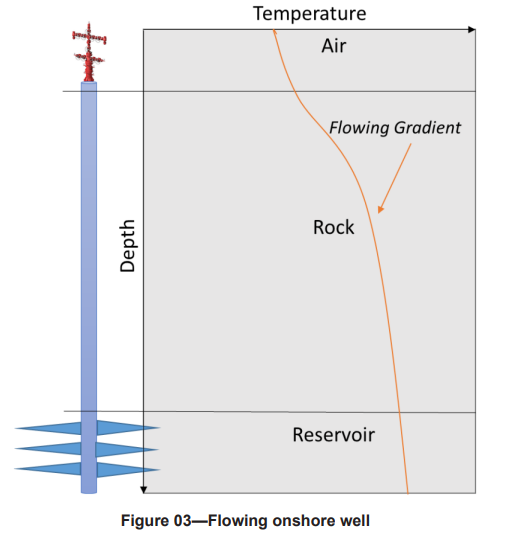
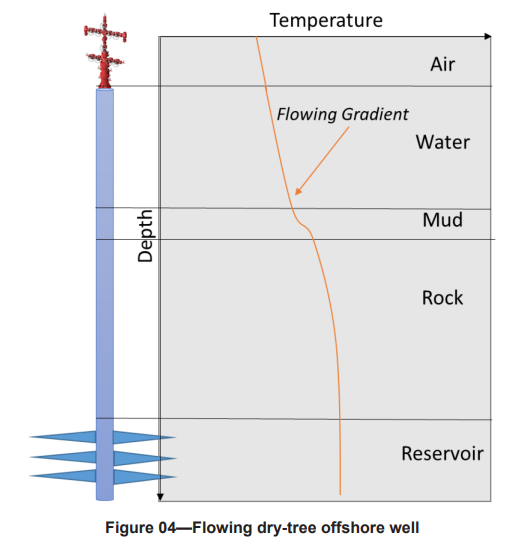
Modes of heat transfer in the well bore – convection, forced convection and conduction
There are two types of convective heat transfer: free (natural) convection and forced convection. A good example of convection is when a well is shut-in and hot fluids from the bottom of the well move up, replacing cooler fluids. In onshore wells, ambient temperature and wind can play a role in heat transfer via forced convection. In offshore wells, conduction and forced convection to/from the water (and the water currents) also play a part in the over-all heat transfer. Heat conduction occurs when heat/energy is transferred between surfaces/molecules/particles, driven by a temperature gradient. This causes heat to transfer to other molecules/particles within the materials or materials in direct contact via vibrational energy – heat transfer occurs from high temperature/vibration molecules/particles to low temperature/vibration molecules/particles.
Overall Heat-transfer Coefficient:
The rate of heat flow from the well bore to the rock/water/air has to be known. In a typical scenario the fluid in the well bore is surrounded by a tubing, annulus, casing, cement and formation rock (the design can vary). This creates a need to have all of the resistances to heat added up to create a single overall resistance and the need to use an over-all heat transfer coefficient.
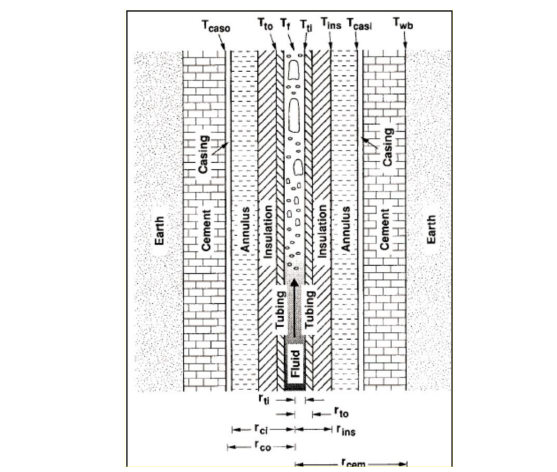
Figure 05 - Heat transfer from a fluid-filled well bore and surrounding formation (Wang 1996)
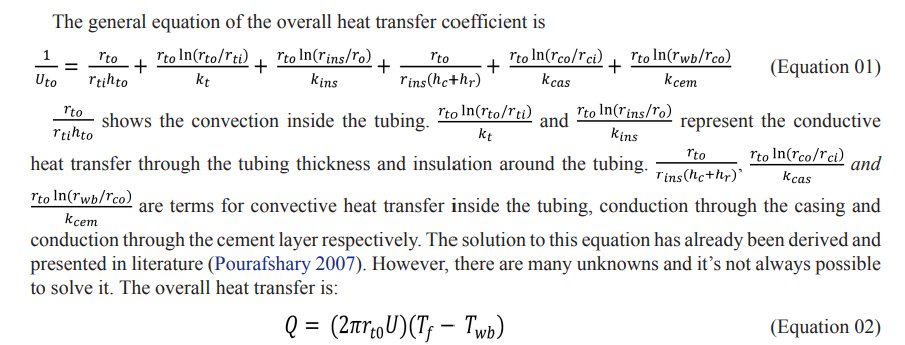
where U is the overall heat transfer coefficient between the flowing fluid and the formation and can be defined as:

Since the temperature difference is changing with time, the rate of heat transfer also varies. The function has an exponential shape and approaches a constant value as the heat transfer between the well bore and formation approaches a constant, at which point the temperature inside the well and in the adjacent formation becomes constant. In the beginning it was mentioned that a dynamic thermalPVT-friction wellbore model will be presented. The need for that stems from the fact that using fluid gradients is too simplistic and does not accurately depict the reality of the transient wellbore behavior. The density mixing of hydrocarbons, the mixing of hydrocarbons with water, and the changing heat capacities of each phase have to be taken into consideration.
Time dependence of heat transfer
In the previous sections the temperature profiles at equilibrium were described. A lot goes on between the time that a static well is turned on until the time that temperature profiles reach equilibrium inside and outside the well. Similarly, the temperature profiles vary with time when a flowing well at equilibrium temperature is suddenly shut-in until thermal equilibrium is re-established. The temperature at any point along the well bore depends on many factors such as fluid composition and the thermal gradient between the mid-stream fluids and the heat sink (formation, water, air, etc.). In addition, the temperature also depends on time. In this section the transient behavior of well bore heat transfer will be discussed.
As a shut-in well is turned on and maintained at a constant rate, reservoir fluids at (or close to) the reservoir temperature flow into the well and travel up the well bore. The well bore temperature is Ta and the temperature in the cooler region (surrounding area at any point along the well bore) is Tb – their difference being ΔT. Heat is transferred up the well bore by the flowing fluid and to the pipe wall and surroundings due to conduction. At every point in the well bore the temperature, Ta, increases but the temperature of the earth, Tb remains the same. ΔT at the bottom of the well (between the fluid at “sandface” and the reservoir) is minimal but it increases as we move up the well since the surrounding formation is much cooler than the produced fluids. As the temperature in the well bore at a given point increases further, the ΔT increases too. One can imagine the temperature difference, ΔT, in the shape of an inverted cone – the bottom of the well being the narrowest and the top of the well being the widest. When the temperatures reach flowing equilibrium, the temperature profile stops changing.
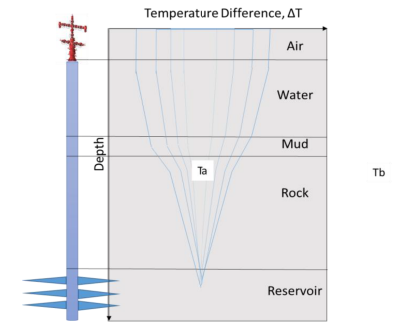
Figure 06 - Changing temperature difference with time between wellbore fluids and surroundings
When any well at equilibrium flowing conditions is shut-in, the wellbore fluids will eventually cool down to the static temperature profile, illustrated in Fig. 01 and Fig.02 in the beginning of this paper. ΔT decreases until Ta becomes the same as Tb for a given depth.
Thermal diffusivity and PVT
Thermal diffusivity is the thermal conductivity divided by density and specific heat capacity at a constant pressure. It measures the ability of a material to conduct thermal energy relative to its ability to store thermal energy. It is a material-specific property for characterizing unsteady heat conduction.
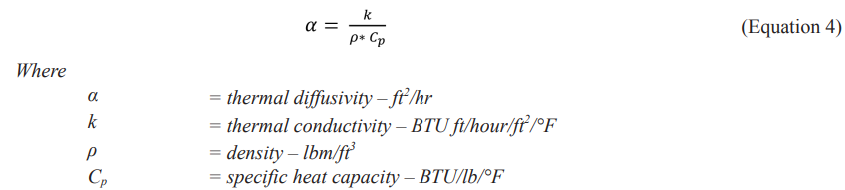
The solution to the thermal diffusivity heat transfer problem (in the r direction in cylindrical coordinates) is the ratio of the time derivative of temperature to its curvature, quantifying the rate at which temperature curve becomes smooth. It is important to mention that the thermal conductivity, specific heat capacity and density of the fluids vary with pressure and temperature. Because all of these terms are grouped together, thermal diffusivity makes it easy to solve transient solutions of the heat equation without having to worry about how the individual terms change with pressure and temperature.
The general heat diffusion equation is (Pourafshary 2007)

where Te is the formation temperature at any depth at time t and r is the radial distance measured from the center of the well. ke is the thermal conductivity, ρe is the density and Cpe is the specific heat capacity of the formation. It is worth mentioning that the thermal diffusivity equation is analogous to the hydraulic diffusivity equation. Instead of pressure, the thermal diffusivity equation has a temperature term and instead of hydraulic diffusivity, there is a thermal diffusivity term. The term is replaced with . It is this term that relates to the change in pressure/temperature with time. The thermal diffusivity of a substance, which is a characterstic property, determines the rate of heat loss of a substance with time.
We assume that when t=0, the formation temperature profile is linear and is based on the geothermal gradient. At the well bore, constant heat conduction is assumed. The well bore is divided into segments and the continuity and energy balance equation are solved in each segment. We can arrive at the solution via numerical integration along the well bore.
Hydrocarbons can mix with other hydrocarbons relatively easily as compared to water. However, at sufficiently high flow rates, we can assume that all phases are mixed and move with the same velocity. Therefore an average of the fluid properties can be computed, and used, based on the constituent phases such as the total flowstream heat capacity. This can be done by building an EOS (equation of state) and determining the Cp of the fluids as a function of pressure, temperature and composition.
Despite various proposed wellbore heat transfer models and correlations, it is almost impossible to know every input parameter corresponding to every well and to accurately solve for temperature at every point in the well under transient and steady-state conditions without real well pressure and temperature data. Given the variety and the large number of wells and well tests that need to be analyzed, it is imperative that a flexible wellbore model (coupled dynamic thermal and PVT model) be used that honors the physics involved and can easily be tuned to match real data. For a linear geothermal gradient, it allows you to determine the temperature at any point along the well if you know the heat loading of the fluid. The thermal diffusivity of the fluid determines the rate of heat loss and gives us the function of how temperature changes with time. As long as the shape of the temperature profile, both static (shut-in) and dynamic (flowing), is known such a model can be created and tuned. The shape of the temperature response can be modeled based on real well data which can be acquired by a flowing and static gradient survey of the well.
Shape And Modeling of the Temperature Response
As important as it is to understand all the mechanisms in play in wellbore heat transfer, it should be mentioned that the measured WHT response is often not representative of the actual WHT of the fluids (mid-stream temperature) at the wellhead. This occurs for a number of reasons such as:
1. The gauge is not in direct communication with the fluid
2. Location of measurement (for e.g. subsea wellhead temperature is often measured at the production head. Sometimes, even if the temperature is measured at the tree, it’s not measured below the mudline)
3. The measured temperature is influenced by external factors like wind, sea currents, sunlight, and surrounding materials having different properties
In such cases, it may not be possible to accurately convert the surface pressures to bottomhole conditions since the surface temperature response is invalid or inaccurate. Therefore, it is crucial to understand the character (shape) of the temperature response to be able to model the temperature and use for conversion of surface pressure to bottomhole conditions. In reality, the temperature at any point along the well bore depends on the fluid composition, the thermal gradient between the mid-stream fluids and the heat sink (formation, water, air, etc.), and time.
Fig. 07 shows the measured temperature response of a gas-condensate well during two shut-ins – one shut-in being longer than the other. The yellow curve and orange curve are measured WHTs during the short and long shut-ins respectively. The gray and blue curves are the modeled WHTs for the short and long shut-ins respectively. The dotted lines are the curve-fitted polynomial functions. The measured temperature decays during the shut-ins and the curve follows the same 6-degree polynomial in both the shut-ins. The curve-fitting in the following examples was performed with a polynomial fit available in standard spreadsheet programs to allow readers to do the same. However, there are other functions that can be used to fit the curve for e.g. logistic, hyperbolic etc. To accurately convert the surface pressure to downhole conditions in a way that it matches the actual downhole gauge response, the wellhead temperature reading needs to be accurate. In this case the measured temperature decays more promptly and reaches a much cooler equilibrium temperature than the actual fluid temperature. Therefore, the converted bottomhole pressures obtained by using this wellhead temperature response and wellhead pressure will not be accurate and will not match the actual downhole pressure.
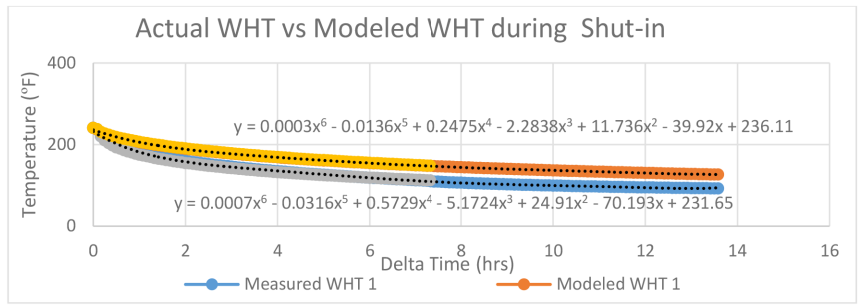
Figure 07 - Measured vs. modeled WHT response for two shut-ins
To accurately convert the surface pressure to downhole conditions in a way that it matches the actual downhole gauge response, the wellhead temperature reading needs to be accurate. In this case the measured temperature decays more promptly and reaches a much cooler equilibrium temperature than the actual fluid temperature. Therefore, the converted bottomhole pressures obtained by using this wellhead temperature response and wellhead pressure will not be accurate and will not match the actual downhole pressure.
To overcome this issue, the thermal response equation can be taken and modified via trial and error until a temperature response that yields an exact match to the measured downhole pressure is obtained. That polynomial equation can then be applied to other shut-ins to model the temperature response. In Fig. 07 please notice that the shape of the modeled temperature response suggests that the wellbore fluids did not cool as significantly during the shut-in as the measured WHT suggests. Similar measurements must be performed at each of the major pivot sections (mud, water, formation, etc.).
Similarly, for drawdowns, the temperature response at each gauge location can be measured and then modeled. The following example is of a gas-condensate well equipped with a wellhead gauge and two downhole gauges. The temperatures were measured during a drawdown and it can be seen in Fig. 08 that the temperature responses follow the corresponding polynomial equations. The measured and modeled downhole temperatures are equal in this case. Should there be a need to model a downhole temperature response based on the wellhead data, the model can be used to convert from wellhead data to downhole data at any point.
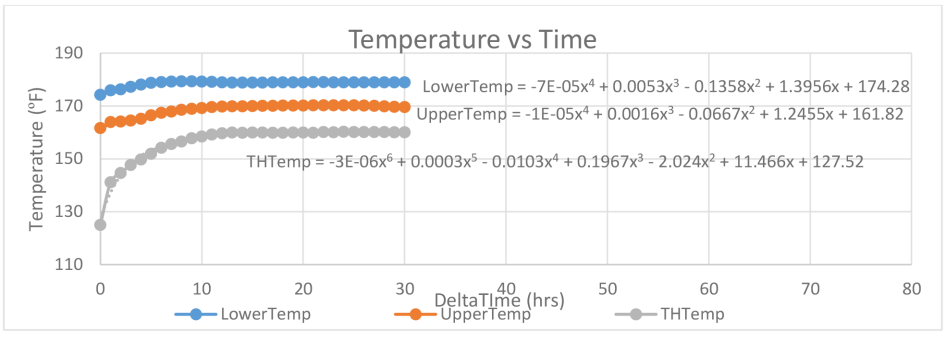
Figure 08 - Measured temperature response during a drawdown in a gas-condensate well
With an understanding of the static temperature profile and the measured response of the well at various points along the well bore, it is possible to translate that response throughout the entire wellbore. The creation of a dynamic thermal model of the well bore can also be done by running a flowing gradient (T, P) survey at different times at constant flow rates. The data in Fig. 09 is from a shut-in in a gas-condensate well. The shut-in temperature curve follows the polynomial equation shown in Fig. 09. Fig 10 shows measured data from another shut-in in the same well. The polynomial equation from the previous shut-in was used to model the shape of the temperature decay. The modeled temperature and measured DHGT overlay one another, confirming the match. The shape of the temperature decay is exponential. However, the solution to the various functions is not always possible. Therefore, by having an understanding of the heat transfer mechanisms in the well bore the shape of the functions can be honored using other equations.
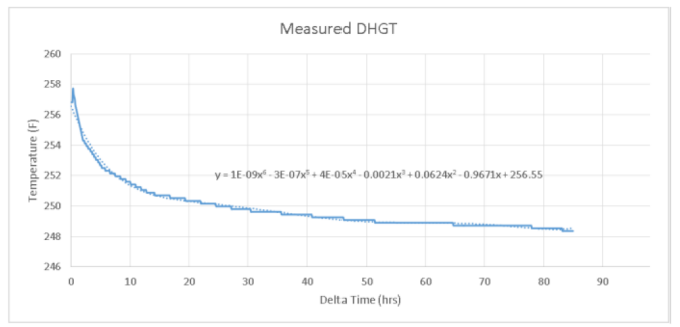
Figure 09 - Measured DHGT with curve fitting
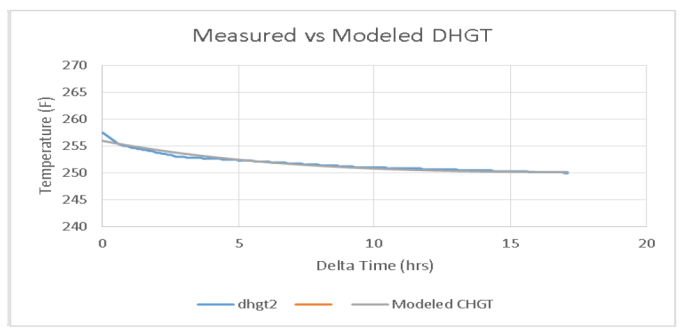
Figure 10 - Measured vs. Modeled DHGT with curve fitting
Wellbore Friction
It is possible to use the Fanning friction factor to calculate the frictional pressure drop empirically. To do so under flowing conditions (assuming the composition remains the same during the process), a pressure drop calibration has to be performed with one or multiple pressure measurement points on/in the well bore. A multi-rate test allows us to measure/calculate the pressure drop along the well bore due to friction at different rates. Thus, the effective friction factor can be back-calculated (assuming the density components of pressure drop are accurately considered).
Impact of Temperature and Friction Effects
This section discuses temperature and friction effects during wellbore operations such as a shut-in, drawdown or a rate change. The combined impact of all of the above mentioned effects on pressure transient analysis results will be discussed toward the end of this section.
1) Thermal transients
2) Impact of temperature on hydrostatic head
3) Well bore friction and boundary layer disruption
4) Impacts of wellbore effects on Pressure Transient Analysis Results
Thermal transients
A temperature transient implies that the temperature is changing and is not constant. When a drawdown is initiated after the well has been shut-in, when a flowing well is shut-in, or when the rate of a flowing well is changed, a temperature transient is initiated. During a temperature transient the density, and therefore hydrostatic head, in the well bore varies both spatially (vertically) and temporally. This change in the head below the measurement point affects the pressure response that is being recorded, and is particularly notable in gas, volatile oil and gas-condensate wells.
During a drawdown, the warming of the fluid during the thermal transient period results in a decrease in density, a decrease in hydrostatic head and a decrease in rate of pressure decay at the surface compared to the rate of pressure decay that is occurring at the mid completion depth.
During a buildup, wellbore cooling causes an increase in density, increase in hydrostatic head and decrease in rate of pressure increase at the surface. Therefore, it is crucial to account for these effects(thermal transients and PVT changes). Failure to do so can result in inaccurate well test interpretation results because the true reservoir response is being masked by wellbore effects.
Impact of temperature on hydrostatic head
For the sake of discussion on hydrostatic head, let’s consider a reservoir with infinite permeability. At shut-in the BHP instantly builds-up to reservoir pressure and stabilizes. As the well bore cools, the fluid density in the well bore increases and so does the hydrostatic head. When this happens, the wellhead pressure must go down. In high permeability reservoirs the rate of increase in BHP during a build-up is low and can be lower than the rate of increase in hydrostatic head due to cooling. This causes the shut-in pressure at the point of measurement to drop. In moderate permeability reservoirs the rate of increase in BHP during a build-up is not as low and it is possible to have the pressure increasing at the point of measurement, but the rate of increase would be lower due to simultaneous increase in hydrostatic head. This will be shown in all of the case studies.
Well bore friction and boundary layer disruption:
Friction along the pipe between the gauge and the perforations plays an important role. During a drawdown, the friction in the tubing between the gauge and perforations causes additional pressure loss and results in a lower pressure being recorded when compared to the actual reservoir/completion response. Using this pressure will result in erroneously high skin and permeability (Fair et al. 2014).
Analyzing bottomhole pressure & impact of wellbore effects on effective permeability and skin factor
Considering all the above factors it becomes clear that to analyze a well test accurately all of the above mentioned wellbore effects need be accounted for. To accomplish that, pressures should be converted to mid-completion bottomhole pressures. Let’s consider the following equationsfor the calculation of effective permeability and skin factor:
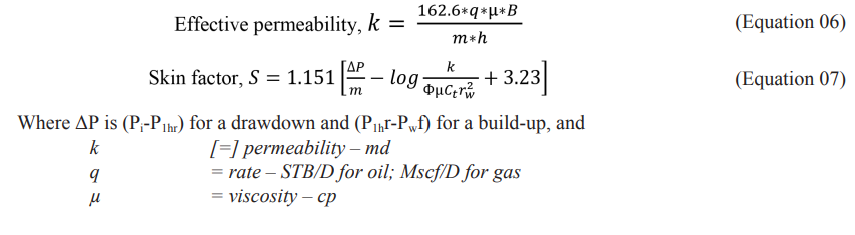
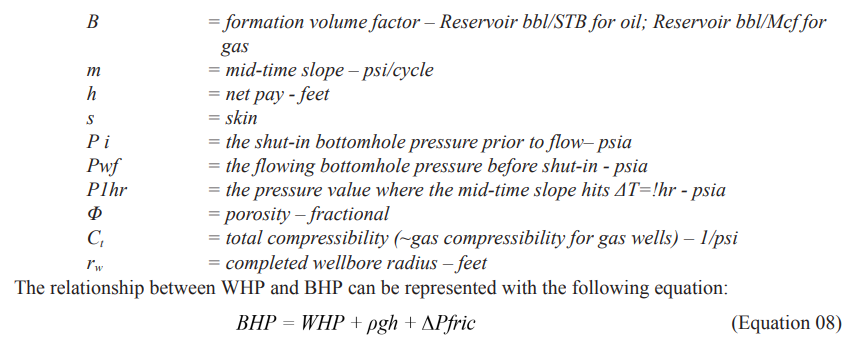
During shut-in conditions, the flow rate is effectively zero, which makes the pressure loss due to friction zero as well. For the sake of discussion, in a build-up the greater interest is in the rate of change in the following parameters:

Although it may seem reasonable to assume that the WHPs and BHPs would be off by a scalar value due to difference in physical location of the gauge (head difference). Thisis not the case for a compressible fluid. The WHP during a shut-in undergoes a decrease in the rate of pressure build-up and the mid-time slope, m (psi/cycle), suppresses. This effect can cause the WHP to become unrepresentative of the reservoir response.
A similar effect occurs when the well is brought on production after a shut-in; warming of the well bore causes the density (and therefore the head) to decrease, resulting in a decrease in the rate of WHP decay, and may even cause the WHP to increase during the wellbore warming period, even though the BHP is decreasing. In this case, the head term in the equation overwhelms the BHP term.
Permeability: The rate of pressure build/decay, otherwise known as the mid-time slope, m (psi/cycle) on the Semi-log affects the calculated effective permeability, k. A smaller (flatter) ‘m’ will result in a higher k and vice versa. During a shut-in, as the wellbore cools the fluid density increases and so does the fluid hydrostatic head. The slope ‘m’ is suppressed due to density effectsin the well bore during shut-in conditions and this yields a higher value of permeability, k at the shallower pressure observation locations. During a drawdown, as the wellbore warms up the fluid density decreases and so does the fluid hydrostatic head. The negative slope “m” is suppressed due to density effects in the well bore and this yields a higher value of permeability at the shallower pressure observation locations.
Skin: It is evident from the skin equation that a smaller m’ value will result in a higher skin value. Another factor that leads to a higher skin value is pressure drop due to friction in the measurement of Pwf, during the flowing period. Due to friction in the well bore below the gauge, the measured Pwf is lower than the actual value and the delta pressure term in the build-up skin equation increases (delta pressure = P1hr – Pwf). This causes the skin value to increase as well.
Estimating P* from pressure build-up tests that are affected by wellbore cooling leads to underestimation of P* due to slope suppression. If the pressure data is corrected for changing fluid density during a shut-in, the mid-time slope will not be as suppressed and will lead to the correct P*.
Methodology
Once it is understood that the phase behavior of the fluids is important and that all fluids are compressible to some degree, it becomes clear that there must be a temperature and pressure dependence of the density (head) and DPfriction in the mechanical energy balance solution to flow in pipes. In addition, as a well bore warms and cools, the temperature at any point along the well bore needs to be predictable. This is a challenging
problem and requires an important, humbling conclusion to be reached before an effective approach can be undertaken: Defeat must be admitted when it comes to knowing all of the unknowns required to solve this problem theoretically. Measurements are required. Computational power must be applied.
In brief, the solution to this problem is a function of the heat capacity and temperature of the fluids entering the well bore from the reservoir (traveling up the well bore), and how this heat is transferred to the surroundings with time via conduction, convection and forced convection. Different portions of the well bore transfer heat in different ways based on which formation or fluid the well bore is opposed to. In addition, the rate of heat transfer is dependent on the amount of the temperature difference between the well fluids and the static temperature of the medium acting as the heat sink. Heat transfer occurs both vertically (via fluid flow and free convection) and radially (via conduction and forced convection). Furthermore, the heat transfer, phase behavior, flow rate, density (and other fluid properties) are inherently coupled and parametric.
Fortunately, the solutions to all of these types of heat transfer problems are known and (even more importantly) the shape of the temperature response given an initial and final condition is known. Therefore, to solve the problem empirically, we need to set up a piece-wise continuous temperature profile for the geothermal gradient,setting pivot points at each of the major differencesin heat transfer (i.e. water vs. mud). We then need to measure the temperature inside each of the major sections during dynamic conditions at a constant flow rate and fluid composition. These measurements can then be used to determine the time-dependent shape of the temperature change. This can then be used to determine the temperature dependence on the heat capacity of the fluid. Thus, as long as the rate and composition of the fluid is known, the temperature at any point along the well bore can be calculated by setting up and solving a segmented thermal diffusivity. If a sufficiently accurate Thermal-PVT-BHP match cannot be obtained by flowing at one rate, 2- or 3-rate testing may be required
Case Studies
Each well in the Case Studies was equipped with a surface gauge and in some cases at least one downhole gauge. The well bore model was used to process the surface gauge pressure data and calculate the pressure response at each gauge depth. This overlay verifies the conversion routine and the PVT, thermal and friction models used in the calculation.
This conversion to each gauge depth was accomplished by using a direct solution to the Mechanical Energy Balance (Bernoulli equation) as opposed to using a vertical lift correlation. The advantage of using a direct solution to the MEB coupled with the thermal and PVT models is that it is more rigorous and can provide more accurate results as long as continuity in the well bore is maintained. On the other hand, most correlations hold true for steady well bore conditions (PVT and temperature) and may not apply to the same well under different flowing conditions. The dynamic thermal model is based on the shape of the function obtained from the numerical integration of the thermal diffusivity along the well bore, along with conduction and forced convection in the mud/seawater/air. The well bore is divided into segments and the continuity and energy balance equation are solved in each segment.
Dry gas well (decreasing surface pressure during shut-in)
The well under discussion is an offshore dry-tree gas well. The mid-completion depth is 8,352’ (MD)/7719’ (TVD). The produced fluid is dry gas (low condensate to gas ratio) that has a gas gravity of 0.69, a condensate yield of 12 BBL/MMscf and water yield of 3 BBL/MMscf. Before the shut-in occurred the well was flowing at a gas rate of 169,079 Mscf/D. Note that the operator did not shut-in the well immediately since it was a high rate well. Therefore, the shut-in spanned over 30 minutes. As soon as the well was shut-in the fluid in the well bore started to cool down and lose energy to the surroundings. As a result, the fluid became denser.
The plot in Fig. 11 contains WHP data recorded during the shut-in. It was observed that the WHPs were decreasing during a build-up which renders the WHP unanalyzable. The WHP decreases in this instance because the hydrostatic head increase was more rapid than the pressure increase from the reservoir. In this case, without the ability to account for the thermal transients and associated density increases the data cannot be analyzed. The wellbore model has the ability to convert the WHP to a representative mid-completion bottomhole pressure, which are depicted on Fig. 11 & Fig. 12 as “aOutDatumPf”.
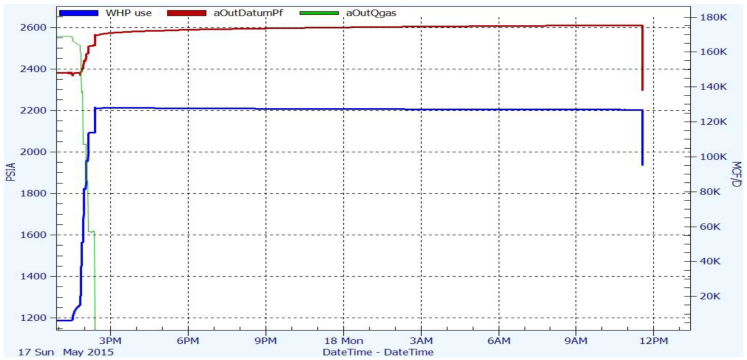
Figure 11 - Cartesian Plot
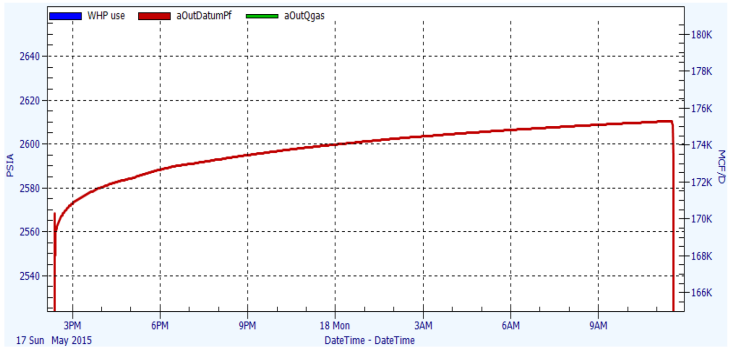
Figure 13 - Converted BHP close-up
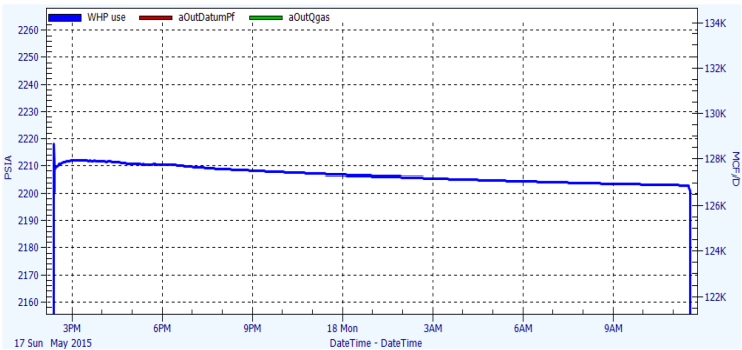
Figure 12 - WHP downward trend close-up
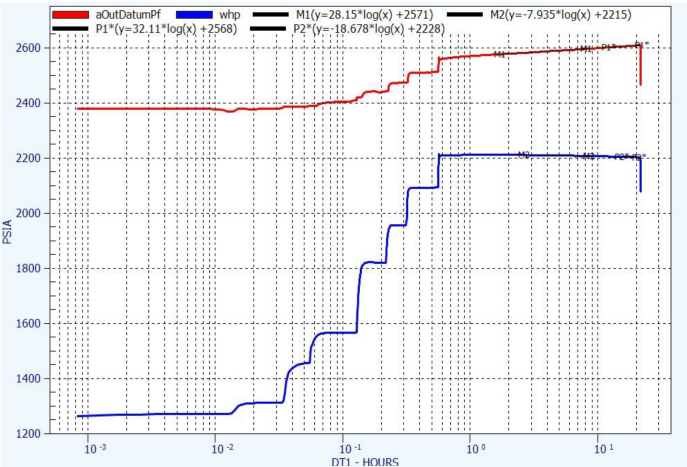
Figure 14 - Semi-log plot
The WHPs were then converted to mid-completion BHPs (aOutDatumPf) and were analyzed to estimate elementary well test parameters. Table 01 summarizes the results of the pressure transient analysis.

Table 01 - Well test results
Fig. 15 contains a plot of the drawdown test prior to the build-up. The rate was increased to 169,000 Mcf/D. The WHP seems to be rising during the drawdown where the opposite is supposed to happen. This is just an artifact of wellbore warming and the fluid column getting lighter due to density reduction. The converted BHP (aOutDatumPf) after taking into account the thermal transient looks more realistic/sensible. The plot in Fig. 16 shows the increasing WHP during the drawdown. Fig. 17 contains a WHP Semi-log plot of the drawdown test. Since the WHP was increasing during the drawdown, this test was unanalyzable using the WHP data. The analysis was performed using the converted mid-completion BHP plot (Fig. 18), as it accounts for changing density due to wellbore warming.
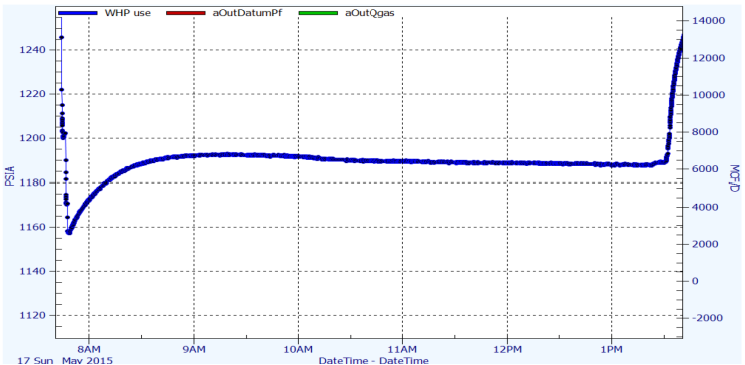
Figure 16 - WHP plot
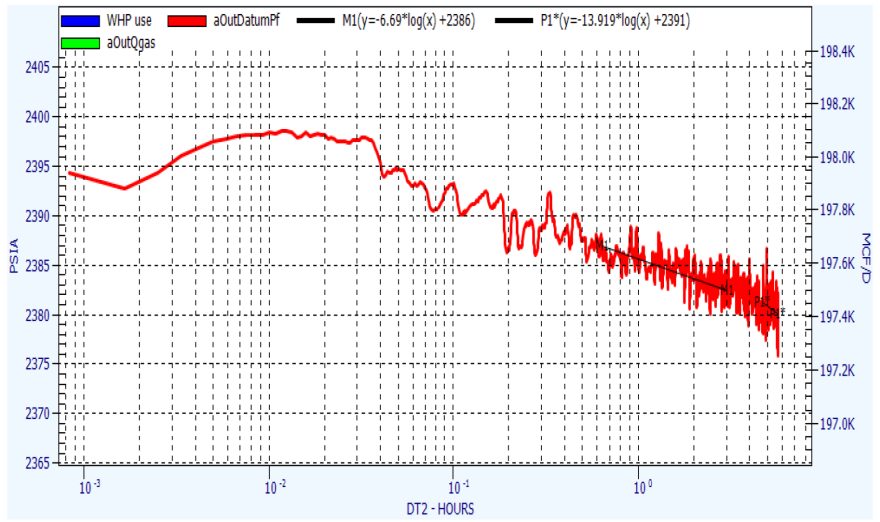
Figure 18 - Drawdown BHP semi-log plot
Table 02 summarizes the results of the drawdown analysis, which are in agreement with the build-up analysis. The drawdown results are different from the build-up analysis results since this well is known to have crossflow.

Table 02 - Well test results
Dry gas well with WHPG AND DHPG
This example is of an onshore dry gas well. The gauge is located at 5,426 ft (TVD) and the mid-completion depth is 6,490 ft (TVD). Fig. 19 contains a plot of wellhead pressure (WHP), downhole gauge pressure (DHGP), calculated pressure at gauge depth (DHGP calculated), mid-completion bottomhole pressure (BHP) and gas rate. Fig. 20 contains a plot of measured DHGP and the calculated DHGP from the measured WHP. The WHP to DHGP conversion was achieved by tuning the gas gravity, and friction. It is evident from the plot that the pressures overlay each other and therefore, the tuning is accurate. Fig. 21 is a Semi-log plot of the WHP, DHGP and the calculated mid-completion bottomhole pressure. Due to the slope suppression caused by the increase in head with time, the mid-time slopes are different from each other, especially the mid-time slope corresponding to the WHP data (143.88 psi/cycle vs 170.93 psi/cycle and 174.23 psi/cycle)
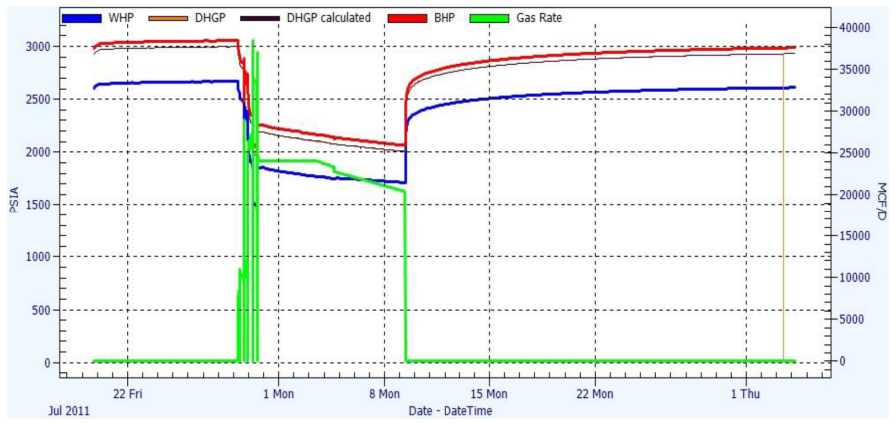
Figure 19 - Cartesian history plot

Figure 20 - Measured and calculated DHGPs
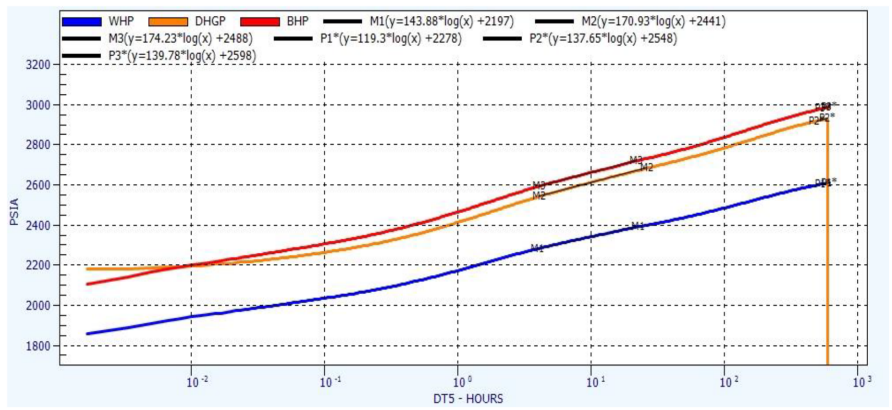
Figure 21 - Semi-log plot
The pressure build-up analysis results can be summarized as follows:
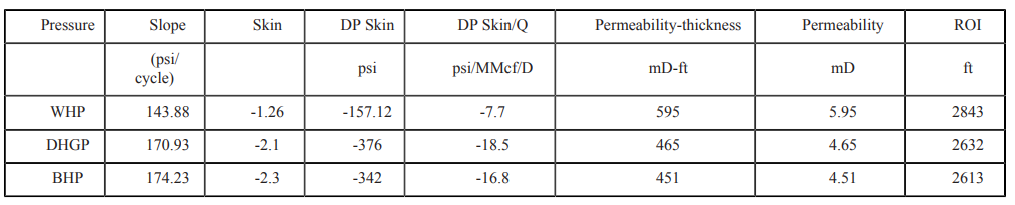
Table 03 - Well test results
It should be noted that the skin, pressure drop due to skin, permeability, permeability-thickness product and the calculated radius of investigation (to the end of test) are all higher as the point of pressure measurement (and analysis) moves up the well bore. This can be misleading since using surface pressures (or DHGPs) for analysis without conversion to mid-completion bottomhole conditions could overestimate the skin and effective permeability and affect other analyses as well as discussed previously. This also highlights that even in low-permeability wells, the effects of thermal transients can play a significant role in the outcome of the analysis/interpretation.
Gas-condensate well (multiple gauge depths)
The data in Fig. 22 shows pressures and rate measurement during roughly two weeks of production followed by a short shut-in in a North Sea subsea gas-condensate well. The pressure was being measured by three permanent gaugesinstalled in the wellbore at different depths. The WHP curve represents wellhead pressure, U-DHGP, located at 5,020 ft (TVD), represents upper downhole gauge pressure, L-DHGP, located at 6,851 ft (TVD), represents lower downhole gauge pressure and Gas represents the rate being measured using a Venturi meter at the surface. The mid-completion depth is 8,743 ft (TVD).
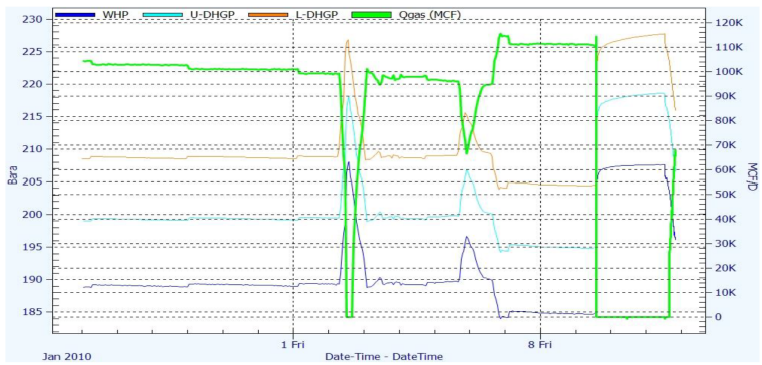
Figure 22 - Cartesian plot of raw data from a gas-condensate well
In this example, it will be demonstrated how the pressure build-up analysis results vary when the analysis is performed using each of the three gauge pressures and then with the converted mid-completion bottomhole pressures. To verify the conversion routine, the WHP was converted to every gauge depth and also mid-completion depth. The calculated pressures at the gauge depths were then compared with the actual measurements. In Fig. 23, aOutTOCP refers to ‘top of completion pressure.’ This was calculated by converting the WHP to the upper gauge depth. The WHP was then converted to the lower gauge depth and called ‘middle of completion pressure,’ aOutMOCP. Then the WHP was converted to mid-completion bottomhole pressure and this was named aOutBOCP. It should be noted that a very close match was obtained by converting the measured WHP to the respective gauge depths when compared to the actual measured gauge pressures. This overlay verifies the conversion routine and the PVT, thermal and friction models used in the calculation. Fig. 24 shows a delta-pressure (DP) plot of the build-up featuring the four pressures (WHP, calculated upper gauge depth pressure, calculated lower gauge depth pressure, calculated mid-completion depth BHP). As can be seen from Fig. 25, the WHP curve (blue) has a higher overall pressure difference and greaterslope suppression than the mid-completion BHP. Fig. 26 shows the Semi-log pressure build-up plots and the corresponding mid-time slopes using the three gauge pressures and the converted mid-completion bottomhole pressure.
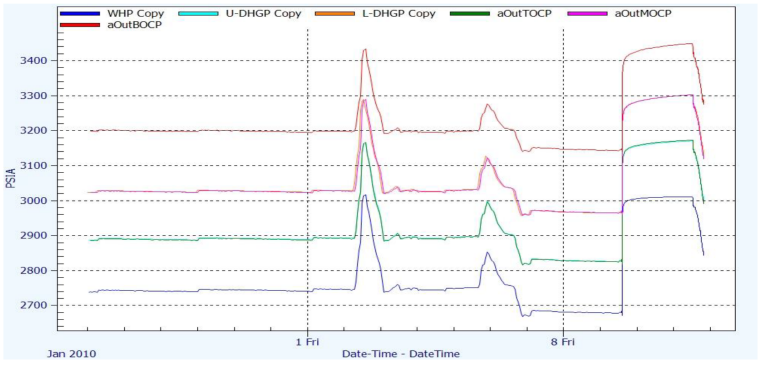
Figure 23 - Cartesian plot of processed data
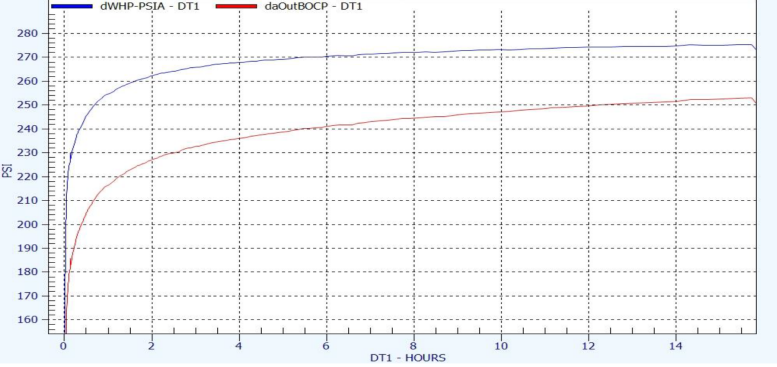
Figure 25 - DP plot WHP and BHP only
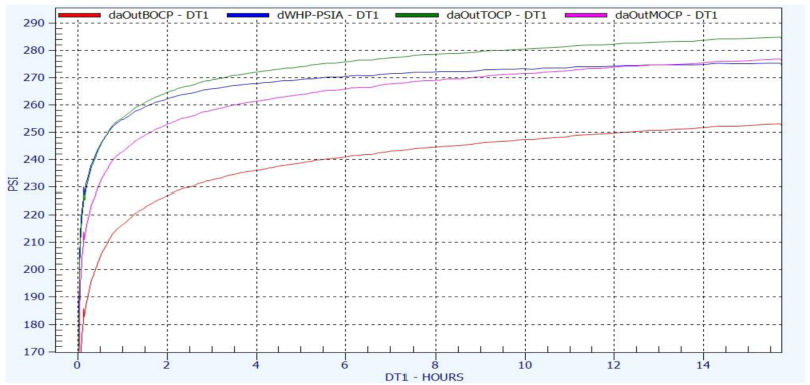
Figure 24 - DP plot
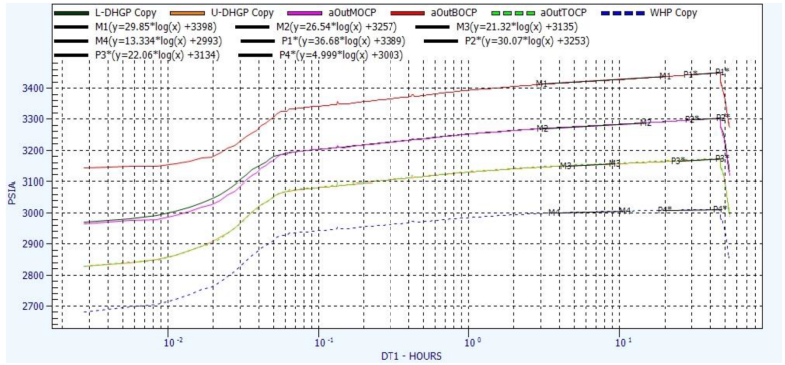
Figure 26 - Semi-log plot
During the build-ups observed in this well, the infinite acting radial flow mid-time slopes (m) on a Semi-log plot were different when plotted on pressure data measured by various gauges at different locations in the well bore; the rate of increase in pressure was different.
The table below summarizes the Semi-log analysis results:
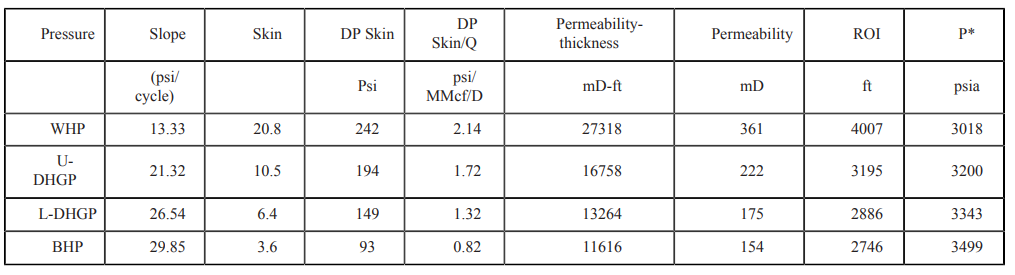
Table 04 - Well test results
The skin using the WHP, U-DHGP, L-DHGP and BHP is 20.8, 10.5, 6.4, and 3.6 respectively. The DPskin/Q (psi/MMcf/D) is 2.14, 1.72, 1.32, and 0.82 respectively. Similarly, the permeability is 361, 222, 175, and 154 mD. It can be noticed that the closer the gauge is to the perforations, the lower the skin appears to be. Also, the rate-normalized pressure drop due to skin decreases the closer the gauge is to the perforations. The calculated permeability decreases with the depth of the pressure observation as well. The estimated P* (psia) using the WHP, U-DHGP, L-DHGP and BHP is 3018, 3200, 3343, and 3499. The estimated P* is lower the further away the gauge is from the perforations.
Oil well (with surface and DHPG)
The following is an example of a subsea oil well located in deepwater GOM. The well has a mid-completion depth of 15,617’ (MD) which translates into 15,567’ (TVD). The well is equipped with a surface gauge and a downhole gauge at 14,659’ (MD)/14,631’ (TVD). The oil has an API gravity of 31º, the bubble point pressure is at 5,395 psi, the GOR is 1620 SCF/STB. The initial reservoir pressure was 11,822 psi. The well was shut-in for a build-up test and the rate before the shut-in occurred was 4,200 STB/D – there was no water production at the time of the test. The fluid in the reservoir and wellbore was single-phase. Fig. 27 contains a Cartesian plot of the WHP. It is evident from the plot that the wellhead pressure during the build-up test was decreasing. This is not a reservoir response but a wellbore phenomenon. The change in density due to cooling occurs quickly enough to mask the change in reservoir pressure and the overall effect is that the WHP decreases making this data unanalyzable. Note that the flowing and shut-in pressures are well above the bubble point, so no argument can be made that this is a phase resegregation effect. Fig. 28 contains a plot of the WHP, DHGP and BHP. It can be observed that the DHGP does not decrease during the shutin, neither does the calculated BHP. In Fig. 29 the WHP is shown to decrease on the Semi-log plot – this renders the surface data unanalyzable. However, the calculated BHP and DHGP in this case have an almost identical mid-time slope value since the DHG is close to the perforations (Fig. 30).

Table 05 - Well test results
Discussion/Results/Summary
Unfortunately, while the fluid mechanics aspects are quite well understood for a variety of flowing conditions (assuming that the rates, phase compositions and PVT properties of the fluid are known or can be calculated accurately), the heat transfer mechanisms are often not included in most of the conventional methods for calculating the mid-completion/datum pressure. The reason for the lack of inclusion of dynamic heat transfer calculations is largely due to “stare decisis” bias – the failure to change because of a previous decision.
Most of these heat transfer problems were solved 50-100 years ago, but require significant computation power to process properly. Hence, correlations were developed and simplified until they could be done by hand, calculator or clunky spreadsheet. Since even these calculations often taxed the engineers doing the calculations, programs based on the correlations were created. As time went along, more and more correlations were developed to “improve” the accuracy of the calculations, then expert systems were developed to pick the best correlation. Along the way, it was forgotten that the often bad assumptions
(including “average temperature”) that were made to make the math simple were still there.
On the other hand, many of the proposed theoretical solutions for dealing with the wellbore/annulus/ formation/water/air heat transfer are overly complex and cannot be solved efficiently (even with today’s processing power). The engineering solution is to honor the physics, but also honor the data!
The method proposed here honors the physics, but recognizes when there are far too many unknowns to be solved without using measurements to create functions that can predict the thermal response of the well as a function of flow rate, composition and time. This predictable thermal response, combined with an EOS and tuned frictional model for the pipe makes it possible to calculate a mid-completion BHP that is representative of the true reservoir response.
Conclusions
Performing pressure-transient analysis on data measured above the completion can lead to inaccurate results and interpretations unless a coupled, dynamic Thermal-PVT wellbore model with tuned friction parameters is used to correct and convert the data to mid-completion bottomhole conditions. If the effects are not corrected, wellbore cooling/heating can overwhelm the reservoir pressure response resulting in decreasing pressure during a build-up or increasing pressure during a drawdown, rendering the raw data unanalyzable. Sometimes these effects are not obvious (for example, the pressure can still build-up, just at a suppressed rate as in Case Study 3) but can still lead to inaccurate PTA resutls.
A semi-empirical method has been developed to convert downhole gauge data, or even surface gauge data, to mid-completion bottomhole conditions such that the calculated response is representative of the true reservoir response. This method honors the physics, but acknowledges the lack of required inputs to solve the theoretical equations. The well bore is broken into sections based on the primary means of heat transfer and is then segmented as needed along the sections to honor the shape of the vertical flowing and
static temperature profiles. It requires a static temperature profile (static survey) and one or more flowing surveys. This data is then used to predict the wellbore temperature profile as a function of heat capacity of the well fluids with time.
Several field examples/Case Studies were presented in this paper, verifying the conversion routine. The raw pressure transient data, that was either suppressed by wellbore effects or was rendered completely unanalyzable, was successfully converted to mid-completion bottomhole conditions for analysis purposes, yielding consistent results with downhole gauge data analysis results (where present). Accurate calculation of true reservoir skin and permeability values can help avoid costly, unnecessary well stimulations (due erroneously high skin), and prevent exaggerated reservoir flow potential and reservoir volume calculations (due to erroneously high perm). More accurate mid-completion pressure calculations also improve the accuracy of static material balance calculations (based on reservoir pressure or P*), and therefore, in-place and remaining hydrocarbon volumes.
These kind of errrors can lead to huge financial mistakes. The physics behind these errors is understood. Just because a gauge’s pressure response increases during a build-up does not mean that the response is representative of the reservoir response. It is no longer acceptable to analyze wellhead or downhole gauge data without correcting for heat transfer and the effect it has on the rate of change of density/head of the fluid below the gauge.
Acknowledgement
The authors would like to thank Stacy Newman for his time and effort reviewing the paper.