With the advent and common usage of high-resolution tree gauges, downhole permanent pressure/temperature gauges, and continuous flow measurement, many of the common petroleum engineering calculations and analysis tools for production systems can and have been automated. These include a) Well Test Analysis, b) Well Productivity, and c) Static and Flowing Material Balances and Energy Balances. In addition, the use of rigorous wellbore thermal and phase behavior models allows the two gauges (wellhead and downhole) to be used as a giant differential pressure meter – making it possible to calculate gas rates and water cuts independently of the flow measurements, as well as mid-completion bottomhole pressure (BHP).
The purpose of this paper is to present the basic physics involved in these calculations/analyses, as well as to discuss the implications that these processes will have on instrumentation selection and on engineering workflows. The crux of the argument for these types of automated systems is that it is much easier for an engineer to check the results than to spend his/her entire day just looking for useful information in the database and then analyzing it (or getting someone else to analyze it). Furthermore, being able to see the “big picture” – seeing what skin, perm, productivity, and apparent hydrocarbon reservoir volumes are now and how they have changed with time, allows engineers to make quicker, more accurate decisions. The use of automated analysis also reduces bias – the computer doesn’t care what the answer is. This paper will also include several case studies for both oil and gas wells.
Using the Results from Automated Petroleum Engineering Calculations to Accelerate Decision Workflows
Copyright 2014, Society of Petroleum Engineers
This paper was prepared for presentation at the SPE Asia Pacific Oil & Gas Conference and Exhibition held in Adelaide, Australia, 14–16 October 2014. This paper was selected for presentation by an SPE program committee following review of information contained in an abstract submitted by the author(s). Contents of the paper have not been reviewed by the Society of Petroleum Engineers and are subject to correction by the author(s). The material does not necessarily reflect any position of the Society of Petroleum Engineers, its officers, or members. Electronic reproduction, distribution, or storage of any part of this paper without the written consent of the Society of Petroleum Engineers is prohibited. Permission to reproduce in print is restricted to an abstract of not more than 300 words; illustrations may not be copied. The abstract must contain conspicuous acknowledgment of SPE copyright.
Abstract
With the advent and common usage of high resolution tree gauges, downhole permanent pressure/ temperature gauges, and continuous flow measurement, many of the common petroleum engineering calculations and analysis tools for production systems can and have been automated. These include: a) Well Test Analysis, b) Well Productivity, c) Static and Flowing Material Balances and Energy Balances. In addition, the use of rigorous wellbore thermal and phase behavior models allows the two gauges (wellhead and downhole) to be used as a giant differential pressure meter – making it possible to calculate gas rates and water cuts independently of the flow measurements, as well as mid-completion bottomhole pressure (BHP).
The purpose of this paper is to present the basic physics involved in these calculations/analyses, as well as to discuss the implications that these processes will have on instrumentation selection and on engineering work flows. The crux of the argument for these types of automated systems is that it is much easier for an engineer to check the results than to spend his/her entire day just looking for useful information in the database, then analyzing it (or getting someone else to analyze it). Furthermore, being able to see the “big picture” – seeing what skin, perm, productivity and apparent hydrocarbon reservoir
volumes are now and how they have changed with time, allows engineers to make quicker, more accurate decisions. The use of automated analysis also reduces bias – the computer doesn’t care what the answer is. This paper will also include several case studies for both oil and gas wells.
Introduction
Over the last decade, improvements in instrumentation quality, data acquisition and transfer, data visualization and manipulation have allowed engineers and managers to view real-time and historic well data with a click of a button. Concurrent with these developments, many of the nuanced problems related to data filtering, processing, and analysis have been solved (or, at least can be solved). However, current practice is to look at the real-time and/or historic data, then export the data to one or more software packages, then re-import the results to the system database/historian. With an engineer’s current workload, this usually doesn’t occur until there’s a problem that needs to be dealt with, which isn’t very proactive. However, by integrating the data acquisition technology with processing and analysis software, the technology now exists to assist an engineer in decision making, even before a well/reservoir develops an obvious problem.
After a quick review of the instrumentation/equipment and data quality issues, this paper will provide a survey of the important physics related to flow in pipes, heat transfer and PVT relationships. Next, well test analysis methods and decline analysis techniques will be discussed, as well as how they can be automated. Special attention will be paid to parametrically solving for flowing and shut-in bottomhole pressures at mid-completion depth (along with the problems associated with not doing so). In addition, using pressure data to solve for gas rate in predominantly gas wells and to solve for water cut in predominantly oil wells will be discussed. Once the rates have been measured or calculated, and validated BHPs have been calculated, the wellbore model can be linked to closed-loop solutions for energy losses in the completion and across the reservoir. This energy loss model allows all three major portions of the “upstream” system to be solved, integrated, and validated in seconds. This rapid evaluation and presentation of results allows an engineer to see the values of critical parameters AND how they are changing
with time.
Background
Pressure, Temperature and Rate Measurements; Data Management
Pressure measurement devices should be selected based on the required accuracy, resolution and thermal compensation (the ability of the sensor to not have the pressure measurement affected by changes in the gauge’s temperature) to adequately observe the response of the well/reservoir. Most sapphire, quartz, piezo and thermally compensated strain gauges manufactured today meet these criteria for low or moderate permeability reservoirs. However, for high permeability (100 md) reservoirs, sapphire or quartz gauges should be used, as they have excellent accuracy and thermal compensation, and usually 0.01
psi or better resolution.
Temperature sensors should be selected based on accuracy and resolution. The accuracy should be /- 1 degree F and the resolution should be 0.1 degree F or better. Most electronic temperature sensors on the market meet these criteria.
Rate measurement devices are much more challenging to specify (aside from the need for the measurements to be digital, and recorded with a time-stamp). Devices range from single-phase, two-phase and 3-phase meters and locations range from the surface to downhole (at least for common oilfield applications). Some commonly used flow meters are:
-
- Orifice/Daniels meters
- Nozzle flowmeters
- Turbine meters
- Venturi meters
- Coriolis meters
- Ultrasonic flowmeters
- Multi-phase flow meters (MPFMs) – some of which are variants of items 1-6
Numerous factors must be considered (besides cost). Chief among these is the answer to the question: What kind of flow AT THE DEVICE LOCATION, NOT STOCK TANK OR SEPARATOR CONDITIONS is expected over the life of the well, over the expected life of the sensor? For example, a subsea multi-phase flow meter would probably not be the ideal choice for a single-phase gas well. . .or an orifice meter would not be well suited for a 3-phase flow system. In addition, for MPFMs, is a simple specific gravity calibration sufficient, or will an Equation of State need to be included; will the calibration
inputs/calculations need to be adjusted over the life of the well? Next, the failure mechanisms and fixes need to be thought-through for each viable device. The accuracy and noise band of the measurements must also be taken into account (resolution is usually not an issue with flow rates).
Once adequate measurement devices have been selected, have been installed and are (hopefully!) all working, the data needs to be sampled at a high enough frequency to digitally reconstruct actual operations. The data also must be transferred to the database without losing resolution – also known as bit dropping. Bit dropping occurs most often during analog to digital (A/D) conversions (18-bit or better is recommended for pressure; 14-bit or better for temperature), especially at the Input/Output (I/O) card on the control panel.
Once the data has made it through the A/D processing in one piece, it can still be negatively altered before it is stored on the database. Before the data is stored on the database, it usually passes through signal filters, archive filters and deadband filters. These filters reduce the time frequency and the resolution of the data being stored. To ensure that that this does not occur on critical data, it is the engineer’s responsibility to specify which data should not be altered.
The fundamental equation for modeling fluid flow in pipes is the First Law of Thermodynamics, also referred to as the Mechanical Energy Balance or the Bernoulli Equation in reference to fluid flow. In its differential form, as presented in Bird, Stewart and Lightfoot1 the equation is:

Where the first term is kinetic energy, the second term is head (DP due to gravity), the third term is the pressure drop, the fourth term is shaft work, the fifth term is pressure loss due to friction and boundary layer disruptions and the last term is losses due to elbows, bends, expansions and contractions in the flow path, and in oilfield units:
v = superficial velocity (ft/sec)
g = gravitational constant (32.17 ft/sec2)
gc = gravitational conversion constant (32.17 ft*lbm/(lbf*sec2)
h or z = height (feet) – true vertical depth/height
p = pressure (psi)
density (lbm/ft3)
Ws = shaft work (horsepower or ft*lbf/sec) – usually supplied by a pump
L = pipe length (feet) – measured depth
Rh = hydraulic radius (feet or inches)
f or ff = friction factor (dimensionless)
ev = friction loss factor (dimensionless)
q = volumetric flow rate (bbl/day or Mscf/D)
D = pipe diameter (inches)
angle formed by the intersection of measured depth and the horizon (gravity term is relative to true
vertical depth; friction is relative to total pipe length—measured depth)
For predominantly phase gas flow, neglecting the insignificant terms, this reduces to:

For predominantly liquid flow, neglecting insignificant terms, the MEB reduces to:

Equation 2 is the basis of the the Cullendar-Smith2 method and other gas-phase correlations/methods.
Equation 3 is the basis of the Beggs & Brill3 and the Hagedorn and Brown4 correlations.
The problem with these correlations (just like any correlation with respect to the data used in its derivation) is that they are only valid over a certain range of temperatures, pressures, PVT conditions and flow conditions. As such, while one correlation might work for one set of a well’s flowing conditions, it may not work for others. Another issue is that these correlations are designed for steady wellbore conditions, most notably PVT behavior and temperature, or that if they do account for these effects, that they do so using other correlations or user-provided inputs. In addition, most correlations do not have an
internal check for continuity.
The Continuity Equation
The continuity equation for fluid flow is listed in Equation 4, which basically says that mass must be conserved (also called the Zeroeth Law of Thermodynamics). The variable ‘t’ is time.
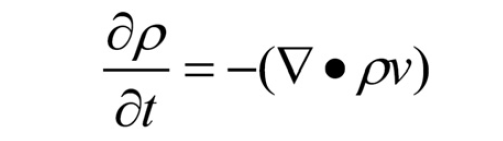
It implies that any mass that enters an element must either leave that element or displace an equal amount of mass. This is fairly simple to visualize in single-phase systems, but it gets a bit more complicated in multi-phase systems. For continuity to hold, there cannot be any accumulation of fluid or of any fluid component in an element (or section of a well bore, for the sake of this discussion). So, with this equation the conditions for continuity can be checked. If continuity holds, then the wellbore system can be mathematically modeled, using a direct solution to the Bernoulli equation (Equation 1). If not, then the well is loading (which is also important to know).
Well Geometry (inside tubing/casing/liner or within the annulus)
In order to model flow in a pipe or annulus, the diameters, measured depths, true vertical depths and materials of construction along the flow path must be known. This information is usually provided in a detailed wellbore and/or completion diagram, accompanied by a deviation survey. It is also useful to know the type of formation, annular fluids/solids, and casing materials along the path of the well bore to assist in heat transfer calculations. Figure 1 presents a well piping model for a highly deviated subsea well in the North Sea.
PVT Modeling – Equation of State (EOS)
An Equation of State (at least for flow in pipe or porous media) is simply a relationship between the pressure, temperature and/or volume of a single component or a mixture of components to that component’s or the mixture’s physical properties. Common physical properties required in flow modeling are viscosity, heat capacity, conductivity, liquid and gas fractions (molar and volumetric), internal energy, molecular weight, Joule-Thomson coefficient, and density. EOS’s can also be used to split the fluid phases into their constituent pure and pseudo-component mole fractions.
The two most commonly used equations of state in the oil industry are the SRK (Soave-Redlich- Kwong)5 and the Peng-Robinson6, both with the Peneloux correction7. There are several commercial software packages available that can be used to generate the variables required for fluid flow modeling. An example of the results from a flash calculation on a black oil well is presented listed in Table 1 and Table 2. A phase envelope is presented in Figure 2.
An EOS is used in detailed fluid flow modeling primarily to avoid the pitfalls of using correlations or simple gradients to calculate pressure drops. This is not to say that using gradients or correlations will always fail; the use of an EOS is just much more rigorous and can deal with changing phases and thermodynamic behavior. With an EOS there are no extrapolations or guesses, the variables are calculated directly.
Thermal/Heat Transfer Modeling
Conduction, Convection & Forced Convection; Wellbore Warming and Cooling
In a production well, from the point where the fluid enters the wellbore to the well head (and beyond), it undergoes heat loss which usually cannot be ignored. In production wells, the fluid entering the well bore from the reservoir is usually hotter than the upper formations which are adjacent to the well bore in which it flows.
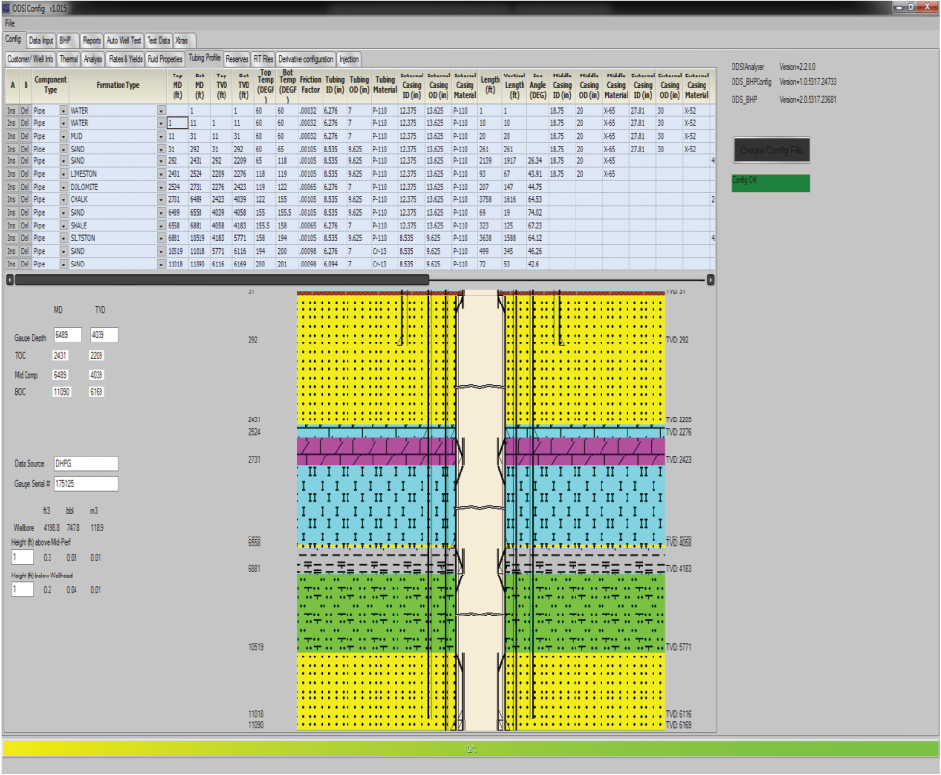
In injection wells the injected fluid may be warmer or cooler than the formations it passes on the way down the well. This heat transfer continues when the well is shut-in. Heat transfers from high temperature to low temperature.
Heat transfer to the formation (or from the formation to the well fluids) occurs primarily via conduction, free convection, forced convection (and to a much lesser extent, radiation), through the fluid media, the pipe walls, the annular fluids/solids, and so on to or from the surrounding formation (for the sake of this discussion, flow behind pipe will not be considered in this discussion).
Conduction is a transfer of vibrational energy (in a quantum sense) by means of molecular agitation/ collision of particles within the material or materials in direct contact due to existence of a temperature gradient. In conduction, the heat is transferred through the same body from one end (High T) to the other (Low T). Conduction can also happen between two bodies at different temperatures are in direct contact with each other. Conduction is the dominant manner of heat transfer in solids, but is also important in liquids and gasses. (Think of putting your hands on a pipe to warm them up – that’s conduction).
Convection is a mode of heat transfer via the movement of fluids. Convection is a dominant mode of heat transfer in liquids and gases. There are two categories of convective heat transfer. These are free (aka natural convection) and forced convection. In free convection, heat transfer takes place when bulk fluid motions are created by buoyancy forces due to changes in fluid density (think of a pot of boiling water).
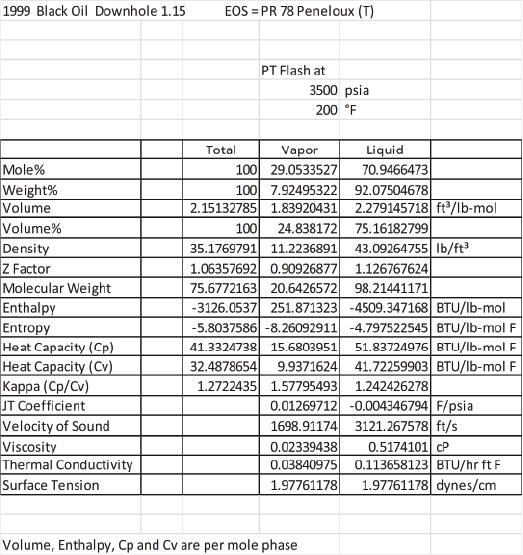
The variations in fluid density occur due to variations in the temperature and/or composition within the fluid. In forced convection, a fluid flow is induced by the external forces such as fans, turbines, blowers, or a well bore (think of the old joke about how an Aggie tells which way the wind is blowing – lick a finger, then blow on it).
When a well is flowing/injecting, friction can also generate heat in/at the boundary layer and the Joule-Thomson effect can cause cooling or warming. Nonetheless, the most important means of heat transfer to or from the surrounding formation are forced convection and conduction. When the well is shut-in, the most important means of heat transfer to/from the formation are conduction and free convection.
For onshore wells, the effects of ambient temperature and wind can also play a role in heat transfer. For offshore wells, conduction and forced convection to/from the water (and the water currents) also plays a major part in heat transfer. Without getting into the intricacies of boundary layers or the nuances of compressible, non-isothermal flow, with this level of complexity, it is fairly easy to see why these problems are solved using heat transfer coefficients – variations on a theme of Newton’s “law” of Cooling/Heating.
There is a vast amount of literature discussing these effects. Fortunately, a lot of effort has been applied to this problem over the last four centuries, and while this is an extremely complex coupling of a large number of variables, these phenomena can be modeled and results can be calculated or adequately approximated. Furthermore, the use of multiple pressure and temperature sensors (or, even better, distributed temperature systems—DTSs), makes the tracking of heat transfer in a system much more rigorous and allows the computations to be performed much more accurately.
With respect to wellbore fluid flow modeling in general, understanding the heat transfer to/from the wellbore is critical to calculating important parameters like flow rate and mid-completion BHP. It is also Table 1—Example of Equation of State Flash Calculation extremely important to solve heat transfer, PVT and wellbore pressure drop (or rate) calculations simultaneously.
Theory
Flow in Pipe/Calculation of Mid-Completion BHP
In order for this series of calculations to work, ALL of the considerations discussed in the Background section must be taken into account simultaneously and parametrically. The measured pressure and temperature dictate the phase behavior at the starting point. The phase behavior dictates the effective density, viscosity and heat transfer. The well geometry and these other parameters determine the velocity at any flow element. The velocity, fluid properties and the state of the pipe-fluid boundary layer determine the frictional losses and the heat transfer. The density and EOS mixing rules determine the head. All of these things change with depth. All of these things change with time. All of these things interrelate!
For a direct solution to the mechanical energy balance to be valid, continuity must hold. The process that is applied in this technique is to first assemble the parametric models for phase behavior and heat transfer (tuning with real well data, if available) and a mathematical construction of the well architecture. The most valid/reliable measurement of pressure must then be selected/isolated and designated a point of continuity. The pressure drop due to rate function can then be calculated in a piece-wise continuous manner (up and down the well bore). This function can then be used to calculate the mass flow rate, given a pressure drop or calculate the pressure drop, given a rate. Once the total mass rate of each component is known, the volume fraction of liquid can be split into oil and water cuts.
It is then critical to calculate the BHP at the mid-completion depth. Failure to do so will often result in an overestimation of permeability (due to fluid density changes caused by wellbore cooling in a build-up or wellbore warming in a drawdown), an overestimation of skin (not accounting for frictional losses upstream of the pressure measurement point) and an underestimation of reservoir pressure (not accounting for head below the pressure measurement point). These problems can be exacerbated during a multi-rate test when the pressure gauge is placed high above the completion or at the surface. Since rate-dependent skin (D-factor) and friction in the pipe below the gauge are both parabolic functions of pressure drop, it is easy to confuse terms in the Forcheimer equation8 for friction in the pipe, often resulting in unrealistic mechanical skin factors (S).
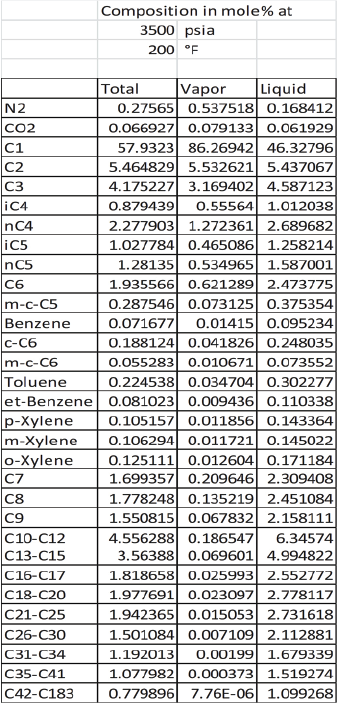
Well Test Analysis
Regardless of whether the preferred graphical/manual method to evaluate a well test (build-up, drawdown, 2-rate test) is a Semi-log plot, a Horner plot or a Derivative plot, automating the process of a well test interpretation involves numerical methods with pointers that tell a computer to look for something it can Table 2—Detailed Composition (pure and pseudo) from EOS Flash calculation use to find kh and skin, productivity (and P* for build-ups).
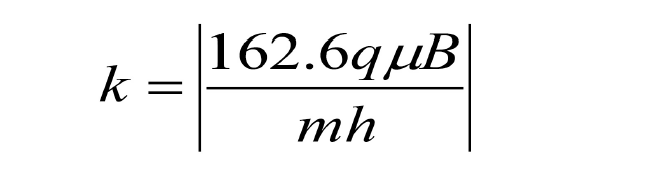
The equation for skin is

ΔP is (Pi-P1hr) for a drawdown and (P1hr-Pwf) for a build-up
k [=] permeability – md
զ [=] rate – STB/day for oil; Mscf/d for gas
μ [=] viscosity – cp
B [=] formation volume factor – Reservoir bbl/STB for oil; Reservoir bbl/Mcf for gas
m [=] mid-time slope – psi/cycle
h [=] net pay – feet
s [=] skin
Pi [=] the shut-in bottomhole pressure prior to flow– psia
P1hr [=] the pressure value where the mid-time slope hits t1hr – psia
m [=] mid-time slope – psi/cycle
Φ [=] porosity – fractional
ct [=] total compressibility (~gas compressibility for gas wells) – 1/psi
rw [=] completed wellbore radius – feet
An excellent discussion of how these are derived can be found in the Well Testing book by Lee10.
P* can be determined either by waiting until enough data has been gathered for an extrapolation of the last slope in the build-up to the extent of the reservoir, or by imposing a model on the data set and using de-convolution methods (although this must be done with extreme caution and with the knowledge that imposing a model sometimes creates the answer that is desired).
The most important thing in this process is that the analysis should be conducted in the same manner every time (unless something happens in the completion or reservoir that changes how the analysis should be done in the first place – adding another zone, shifting sleeves, post-production frac’ing, etc.). In this way, an engineer can focus on the changes in skin, permeability and reservoir pressure.
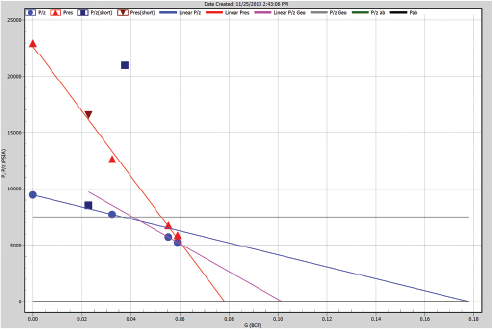
Productivity and Inverse Productivity
Productivity Index is simply the rate divided by the delta pressure from the mid-completion BHP out to some distance in the reservoir (DP Preservoir – BHP). Depending on the geometry of the well, the configuration of the reservoir, the location of other wells in the same reservoir, and a host of other factors, this distance can vary from method to method and from engineer to engineer. To be honest, the method chosen really doesn’t matter much – the way that it changes is what matters. . .that, and the ability to consistently calculate the reservoir pressure at the selected distance. Inverse Productivity (IP) is the reciprocal of the productivity index. Due to the variability in the methods for determining the reservoir pressure described above, it is also common practice to calculate relative PI and relative IP. This is accomplished by setting Preservoir to the initial reservoir pressure.
Nodal Analysis
Nodal Analysis is the combination of a vertical lift performance (VLP) function with a reservoir inflow function, also called an Inflow Performance Relationship (IPR) or Curve (IPC). Ideally, the reservoir permeability used as an input for the reservoir inflow function is obtained from the last valid drawdown well test analysis (or from the last build-up, if there are no problems with fluid re-segregation, multiple formation layers with crossflow, rock compressibility effects, or temperature-related density changes below the pressure gauge). However, in practice, either the permeability or the skin are estimated (quite often, with bias) and the other parameter is then solved for. . .often using a misapplied IPR function (i.e. transient for steady-state or vice versa). Without getting into the pitfalls of having to pick from hundreds of VLP correlations, the biggest problem with nodal analysis is that the nature of the inflow performance relationship is that there are an infinite combination of skin and perm values that lead to the same pressure drop (Preservoir-Pwf). If used in isolation, this can lead to the improper diagnosis of a well problem – thinking it has a skin problem, when it really has a perm problem or vice versa.
P/z, Static MBAL and Flowing MBALs and EBALs
A P/z plot (shown in Figure 3) for gas wells or a Static Material Balance for oil wells provide a means to evaluate the total elastic energy in a reservoir. This volume is then translated into an oil or gas volume to find the in-place volumes and with an abandonment pressure to determine the maximum recoverable volumes under a likely economic limit. The biggest problem with these calculations is that they are counting EVERYTHING. . .gas, oil, water, and elastic energy in the rock, i.e. anything that can move, wiggle or expand. This is why it is considered bad practice to use a P/z plot on gas wells with known water drive. By applying another extreme case – that of Straight-Line Depletion (SLD), with hydrocarbons being pushed by an infinite aquifer – a minimum in-place hydrocarbon volume can be obtained. This case assumes that there is no expansion of the hydrocarbons. These two cases then provide the bookends to the range of possible hydrocarbons in-place.
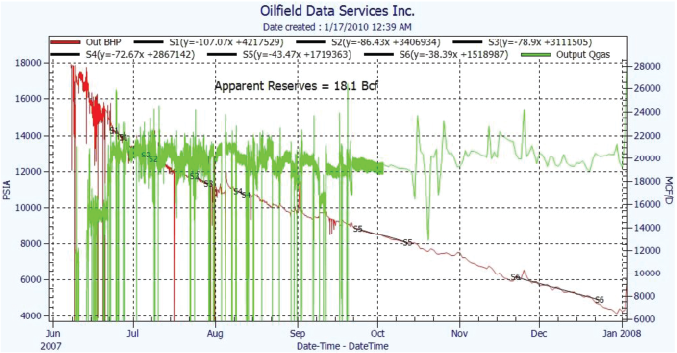
A Static Material Balance makes use of the relationship between decreasing reservoir pressure as a well/reservoir is produced and the ability of the remaining fluid to expand to occupy the same pore space. Like the SLD volume versions of the decline analysis methods, a straight-line depletion calculation may also be applied here, determining the apparent oil volume if it is being displaced in a piston-like fashion by an infinite aquifer.
The SLD Static MBAL equation for oil wells above the bubble point is:

Where N Volume of oil in reservoir (STB), Np Produced Volume of oil at time where P|Np was determined, Pi initial reservoir pressure (psia); P|Np reservoir pressure corresponding to produced volume, Np.
The compressible form of the Static MBAL equations for oil wells above the bubble point is:

Where N Volume of oil in reservoir (STB), Np Produced Volume of oil at time where P|Np was determined, Boi oil formation volume factor (FVF) at Pi; Bo|Np oil FVF at P|Np
Flowing MBAL: SLD and Compressibility Volume
The compressibility volume is determined using the rate of decay with pressure per unit time (i.e. PSI/day) on a Cartesian plot. If a reservoir is in a closed system and once all of the boundaries of the reservoir are encountered, the well will then transition to some sort of steady-state flow (usually PSS). Figure 4 is a plot of DP-DT – also known as a Conventional Decline Analysis Plot.
The equation for compressibility volume is:

The SLD (Straight-Line Depletion) form of the equation is:

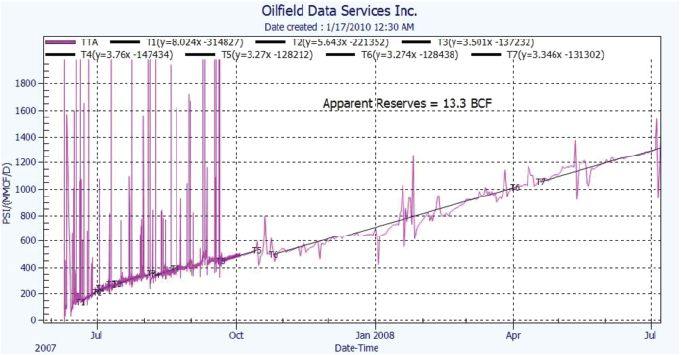
VSLD and Vc = volume in units compatible with Qavg & DT, Qavg [=] average flow rate over the period where the DP/DT-slope is selected, DP/DT-slope is the decline in pressure per unit time [=] psi/day, and Ct is total system compressibility (1/psi).
TTA Evaluation: Coupled Rate & Pressure Decline Analysis
TTA is the acronym for Thermodynamic Transient Analysis. It refers to any technique of analysis that applies the constant driving force solution of the diffusivity equation. (Note PTA – Pressure Transient Analysis is the solution with rate as a constant, RTA – Rate Transient Analysis is the solution with pressure as a constant). TTA allows both rate and pressure to decline and is employed either by itself or in conjunction with one of the other two methods, using average rate (constant) or average pressure (constant) to perform well test analysis for low-permeability wells during a drawdown or to determine the mobile volumes of the compressible phase in the reservoir.
The TTA function is simply the relative inverse productivity: (Pinitial-Pwf)/Qspot. Pinitial is a constant – initial reservoir pressure. To get to the equations used for TTA vs. PTA, all that needs to be done is to set the boundary conditions such that the rate decline is linear. Furthermore, the assumptions about declining pressure and the effect on fluid properties used in the constant rate (PTA) derivation of the diffusivity equation apply here as well. Figure 5 presents a TTA plot.
If the right conditions are met and the right boundary conditions are set up, the compressibility equation can be altered via an algebraic substitution, based on the hypothesis that the difference between the conventional results and the TTA results is the difference between the classic Energy Equation and the solution to the classic Energy Equation with the higher order terms included. This is why there is a difference in the two calculations if both pressure and rate are dropping during a drawdown. The same substitution can be applied to the SLD equation.
The TTA compressibility volume (mobile hydraulically connected volume):


where the TTA-Slope has units consistent with the stock-tank or standard condition rate units and pressures.
Infinite Aquifer Boundary Condition
While the use of the compressibility volume provides a calculation of the connected and mobile hydrocarbon volumes, the use of straight-line depletion (conventional and thermodynamic) provides the other bookend on the conservative side of the estimated hydrocarbon volume. It assumes that there is no depletion, only displacement of the oil by an infinite aquifer. The conventional SLD method does not account for inertial losses (energy used-up transferring fluids from one point to another in the reservoir
that is not related to “permeability”); the TTA-SLD method does.
These four equations (Equations 9 a-d) and how they change with time form the basis of the decline analysis.
The interpretation of the slopes derived from a producing well is fairly straight-forward – all of the boundaries of the reservoir need to have been encountered by the radius of investigation (usually 4-ish boundaries, depending on the contact angles of the boundaries) and then observed closure and the transition to some sort of steady-state flow. It should be noted that one or two boundaries may be HC-liquid contacts, as long as there is no or little observed influx from the aquifer. Given that there is no way to be absolutely certain that there is not water influx, the Straight-Line-Depletion volume can be calculated to approximate an infinite aquifer on the edge of or beneath the hydrocarbons and obtain the
minimum volume.
Application and Automation
These calculations and methods generally fall into categories answering the following questions:
-
- What is going on in the well bore?
- What is going on in the completion?
- What is going on in the reservoir?
The equations for calculating skin, permeability and reservoir pressure have been around for decades, as have the equations for reservoir inflow. Other than the use of de-convolution and moving boundary conditions, there really hasn’t been much change in how completion and reservoir behavior are evaluated or predicted since Hurst11 (although more horsepower in a computer does speed things up a bit). However, without valid rates and BHPs, answering the second and third questions above is extremely challenging. Hence, modeling what is happening in the well bore is the linchpin to sorting everything else out.
Assuming that there are no problems with the sensors, and that the IT department isn’t culling or filtering out data, nor truncating resolution or deadbanding the readings, the first step is to validate the pressure readings, then to validate and/or calculate the mass flow rate. If this fails, it means the system is not continuous and is likely loading-up in the well bore; a valid BHP cannot be calculated. If this process converges to a solution, a valid rate for each phase (both in-situ and at stock-tank conditions can be obtained) and a mid-completion BHP can be calculated.
Once valid rates and BHPs have been calculated, PI and IP can be calculated continuously. Transient recognition of build-ups, drawdowns and 2-rate tests can then be applied to search for potential well tests to analyze. If the transient meets the conditions required to attempt an analysis, they can be automatically analyzed and updated as more data is recorded. If the analysis is not accurate (for example if a build-up stops before it reaches radial flow), it can be automatically or manually deleted from the well test history.
Once the well reaches steady-state of some sort (semi-, pseudo-, frac-dominant-, etc.), the flowing material and energy balances may then be calculated. If a well is shut-in long enough to achieve a valid P*, a static material balance (P/z for gas) can be performed. If any of the boundaries appear to be gas-liquid or oil-water contacts, they can be flagged and their movements can be tracked with subsequent
well tests.
The work flow for using these results is a transformation of the current way of obtaining results. Automation of these calculations and the presentation of the results shifts the focus of an engineer away from the tiring and tedious activity of digging through the database to gather the required data. . . then organizing it, analyzing it, and then maybe figuring out what it means. . .and what (if anything) should be done; then going through the process of finding someone with the authority to do something about it. . . Toward checking/validating the results and reaching conclusions, with documentation already provided.
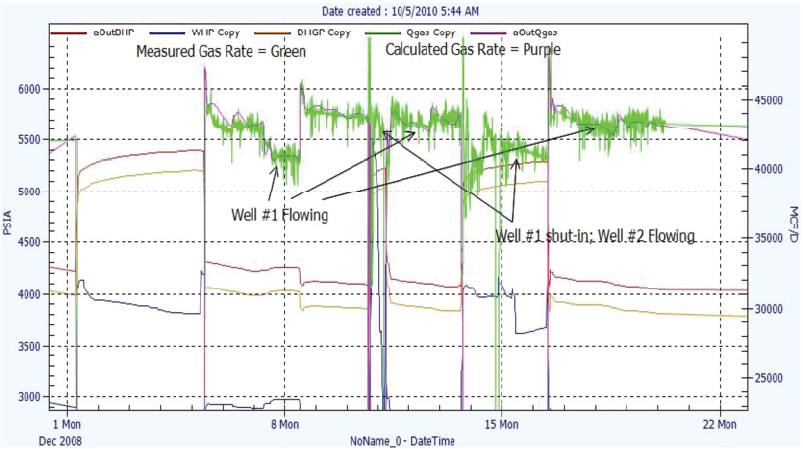
In addition, since the same information can be viewed by other more and less experienced engineers and managers, everyone can look at the “big picture” instead of just their own little silo. This allows younger engineers/managers to be involved in the decision making process (or at least witness it), as well as learn from more experienced engineers/managers and technical experts. This democratization of the results of well/reservoir evaluations also makes it much more likely that decisions will be made in the first place, simply because no one “owns” or is responsible for the results (or for making a mistake), so the fear of bringing up a problem is overcome by it being very difficult to figure out who to blame. It should also focus attention toward the following questions:
-
- How much money/NPV is left in the well/reservoir?
- Are there any potential problems in the well bore (loading, scaling), completion (skin, screen plugging) or reservoir (rapid depletion, formation compaction, water encroachment)?
- Is there anything that can be done to improve the NPV of the well?
- What should be done if something unexpected (especially bad!) happens?
Case Studies and Results
The following Case Study (CS #1) is for a subsea gas well in the North Sea. The well is equipped with both downhole and wellhead gauges, measuring pressure and temperature. Multiple subsea wells flow to the same meter at the host platform, where gas rates for the field are determined, but individual well gas rates are not known when multiple wells are flowing.
For this well, the objective was simple: Calculate the gas rate and look at the build-ups for signs of depletion. Figure 6 shows the comparison of this well’s measured rate vs. the rate calculated from the d/p in the well bore during a period when it was the only well flowing. The results (aside from a little more noise in the metered rate) are identical.
Figure 7 shows the results of multiple build-ups tests over the course of several months of production.
The analyses show little change in skin or perm, so there have been no changes to the completion or formation. However, it appears that reservoir pressure has dropped over 1500 psi in the course of six months. The reservoir appears to be depletion drive or weak water drive.
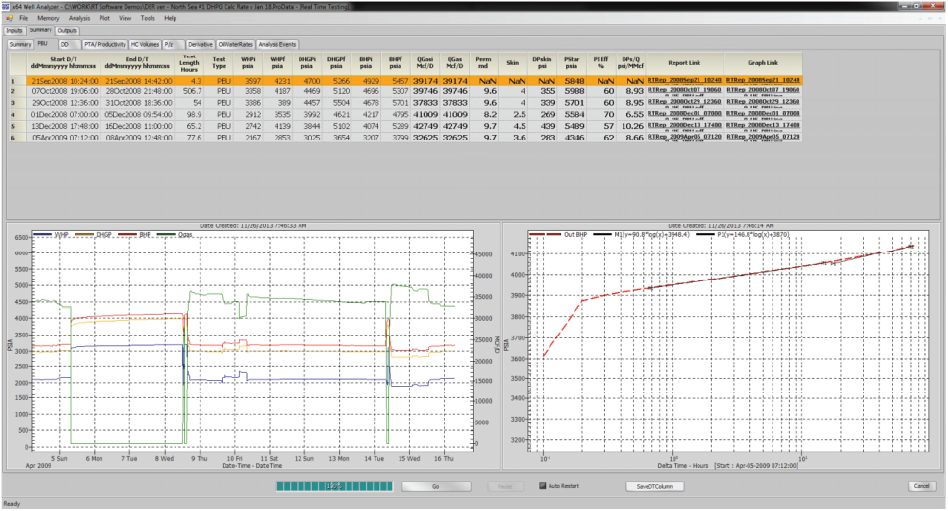
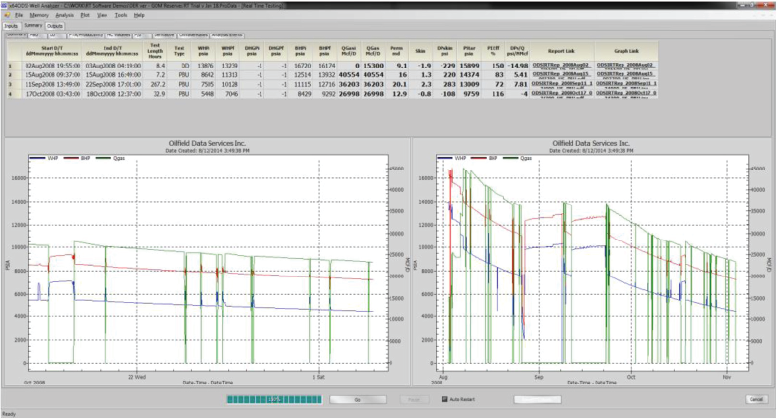
The following Case Study (CS #2) is from a HP/HT gas/condensate well in the Gulf of Mexico. The well had a Scada WHP gauge and a dedicated separator, with the ability to measure gas rate instantaneously and liquid rates periodically. With this set-up, a residence time lag had to be applied to get effective spot rates, as using the direct turbine meter data would be erroneously high or low, depending on whether a dump was occurring. Once the rates were validated, the BHP at mid-completion depth was calculated. The data was also screened for pressure transients; if found, these were analyzed for skin, permeability and P* (for build-ups). Figure 8 shows the results of this process.
The well test analyses (although there is a bit of variance) indicate that the permeability is around 15 md and the skin was low and stayed low for each of the subsequent tests. The reservoir pressure also appeared to have dropped over 6000 psi during the course of the test, so it looks like the well is in depletion drive.
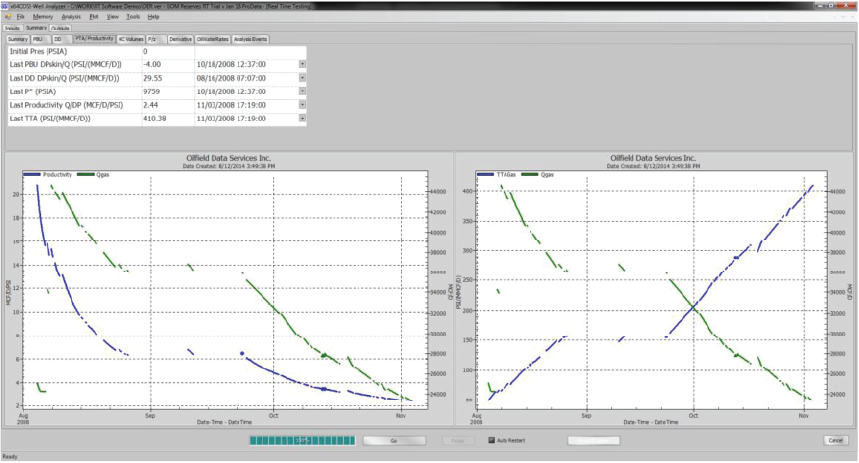
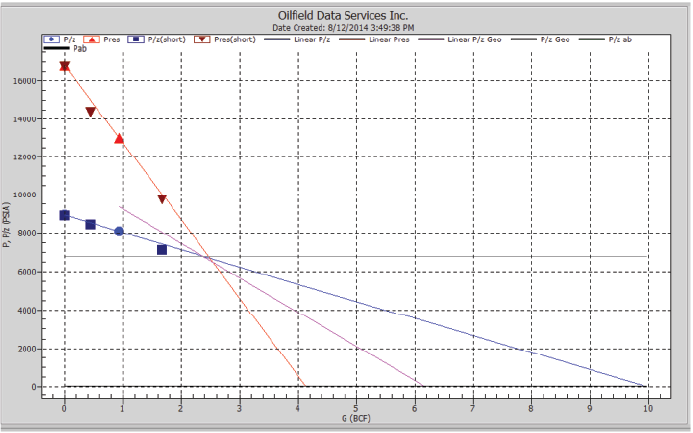
depletion drive. Looking at the relative PI and IP plots in Figure 9, it also appears that there are no big changes in well performance with time (no shifts in scalar value and no changes in slope). It also appears that the relative IP function is linear, so it is likely that the well is in some form of steady-state flow.
In Figure 8, there are two long build-ups, and the cumulative gas volume has also been determined, so it is possible to perform a P/z and an SLD-P calculation to get the range of possible in-place gas. Figure 10 shows this plot, resulting in a range of 4.0 to 10.0 BCF.
Running Energy and Material Balances can also be performed; Figure 11 shows a plot of the various functions. The LHS shows the remaining apparent gas volumes; the RHS shows the total gas volumes, which can be compared to the P/z results. Please note that the gaps are due to rate adjustments, shut-in and other transients that disrupt the steady-state flow regime in the reservoir, which are shown in Figure 8.
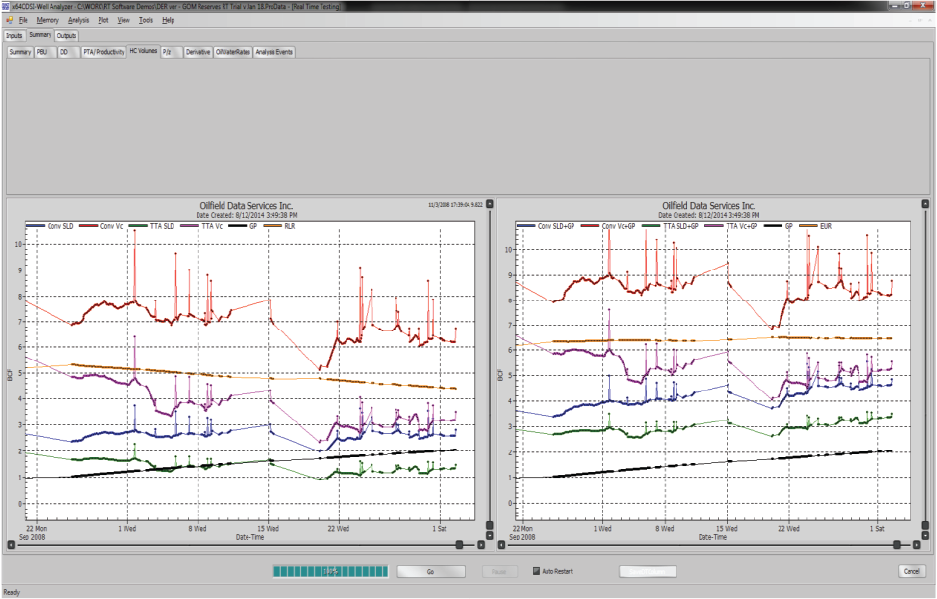
The LHS of Figure 12 shows the two bookends – SLD (red) and P/z (blue). Recall that SLD is for the boundary condition of a hydrocarbon volume on top of an infinite aquifer and that P/z is for the case of just expansion/depletion drive. The RHS displays the conventional compressibility volume (red), the conventional SLD volume (blue), the TTA compressibility volume (purple) and the TTA-SLD volume (green). The black line is Gp the cumulative gas production. The yellow line will be addressed shortly. Recall that the difference between the TTA function and the conventional DP-DT slope is that the TTA is looking at mobile compressible fluids and the DP-DT is looking at hydraulically connected energy. In addition, the compressibility volume versions of these functions are based on expansion; the SLD versions are based on displacement, not expansion. It should also be stressed that the hydraulically connected volume counts ALL connected elastic energy, not just the gas phase.
Furthermore, the SLD functions are also relative functions. The absolute values matter (they relate to the minimum producible volumes of the compressible phase), but the relative change with time matters more, as they are indicative of changing boundary conditions in the reservoir, which can be used to split the total elastic energy into its constituent components. For gas and gas/condensate reservoirs, the change in the conventional SLD (blue) relates to water encroachment and the TTA-SLD (green) relates to rock compaction.
The yellow function result is the static material balance out to the point of the gas/water contact. Gas/water contacts have characteristic responses when struck by the radius of investigation. Once detected, its position can be tracked and the water volume can be excluded from the overall apparent volume.
To summarize what is known about this well/reservoir: It has produced roughly 2 Bcf of gas and has depleted approximately 6000 psia. It has permeability around 15 md and a skin around zero. The relative inverse productivity indicates that the well is in steady-state flow, with little change in the slope and no shifts in the scalar values – so, no significant changes in apparent volume or completion quality.
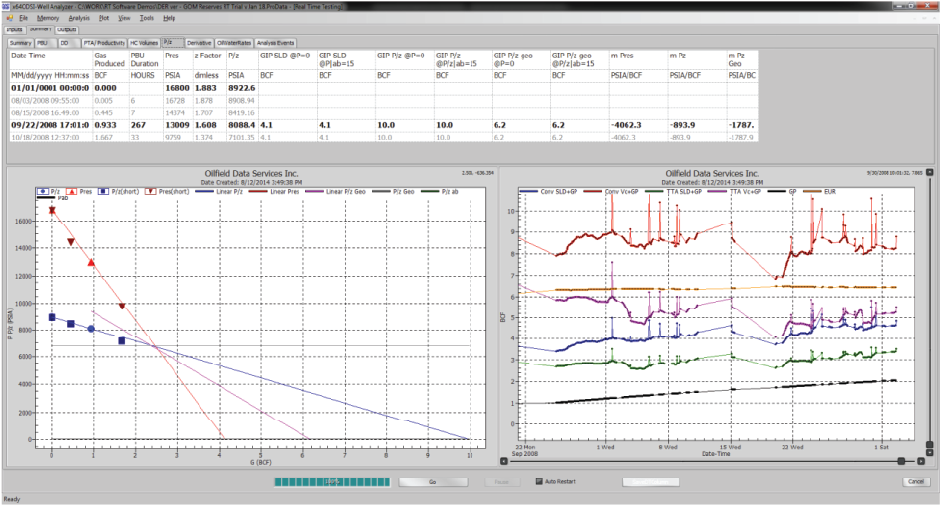
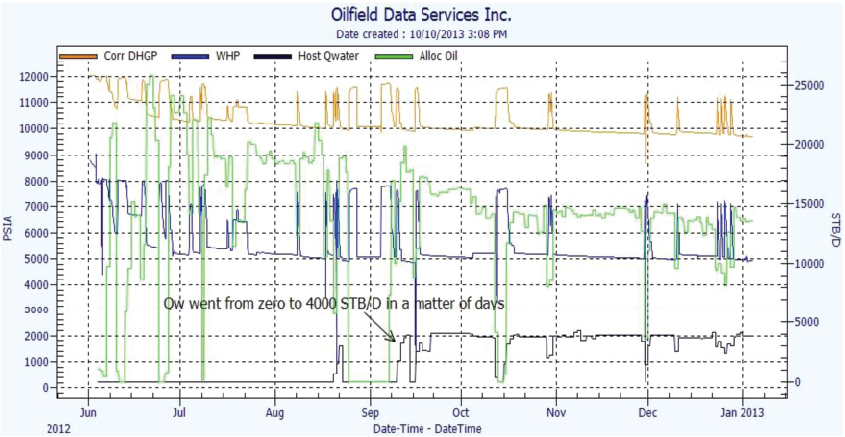
The apparent initial reservoir volumes range from the build-ups is from 4.0 to 10.0 BCF. The initial hydraulically connected volume was between 8-9 BCF, of which 5-6 BCF is mobile gas. Of the 10 BCF of total elastic energy (from the P/z), about 3 BCF of gas-equivalent volume is water in a dead-leg and about 1 BCF of the gas-equivalent volume is due to rock compaction. The water-tracking material balance (yellow) indicates a maximum in-place gas volume of 6.5 BCF (1 BCF of which could be rock compaction).Thus, everything points to this well making around 5.5 BCF of gas (assuming that the completion doesn’t experience shear failure due to rock compaction). So, regardless of how many BCF are “on the books”, 5.5 BCF is what should be used for economic decisions.
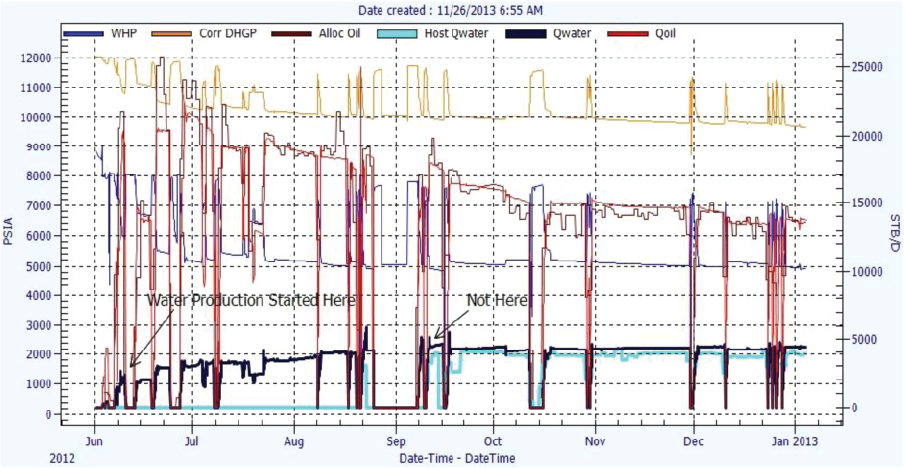
Case Study #2 Work Flow Example
Suppose that this is your well and it is producing 25 MMscf/D and 500 STB/D of condensate, having already made 2 BCF of gas and 40,000 STB of condensate. Then, overnight the pressure jumps and the well turns into a geyser, making 8000 bbl of water per day and very little gas or condensate. You have 3.5 BCF and 70,000 STB of condensate left in the reservoir. You can do the math in your head and start running in hole to find out where the water’s coming from (and start preparing the AFE to go perforate and squeeze that water zone that looked like bad news on the CBL).
Suppose that the well starts making some water around the time the well has a Gp of 3.5 Bcf, starts having loading problems around 5.0 Bcf, then loads-up and dies at 5.3 Bcf. You can do the math in your head – you’re done with this zone.
Case Study #3
CS #3 is a review of automated processing of historic data to settle an argument regarding a subsea deepwater GOM oil well. Partner A got into a panic because their rate allocations showed a sudden spike in water rate from zero to 4000 STB/D and wanted to rush out to do a multi-million dollar intervention to stop the water production. Partner B wasn’t so sure that this was a brilliant idea. The subsea and downhole gauge data was then processed from the beginning of the well’s production life to determine the water cut. Figure 13 shows the well pressures and the allocated rates.
The water and oil rates were then processed using the techniques described in the wellbore modeling section of this paper, resulting in the rates presented in Figure 14.
It turned out that the problem was that the MPFM was improperly calibrated and that the separator testing methods were poor. Water production began when the well first came on-line, not when the allocations indicated.
In Case Study #4, the operator of a new volatile oil well in the GOM wanted to know as soon as possible after the start-up of a new producing well, if an injection well was warranted in the reservoir. The well had a dedicated separator to measure oil, water and gas rates, and a high-resolution Scada gauge to measure WHP.
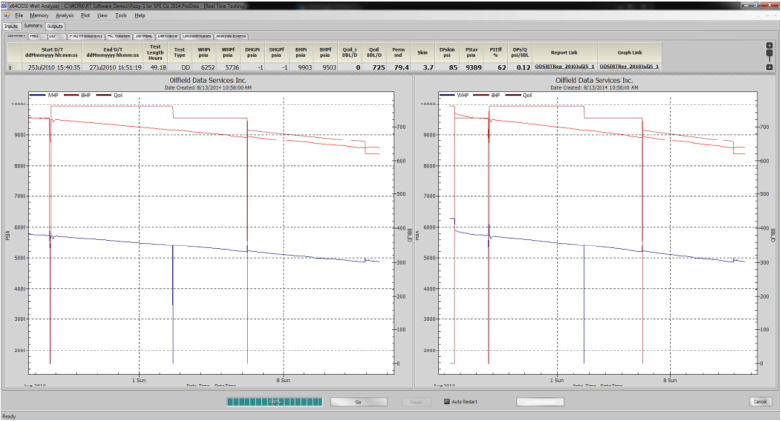
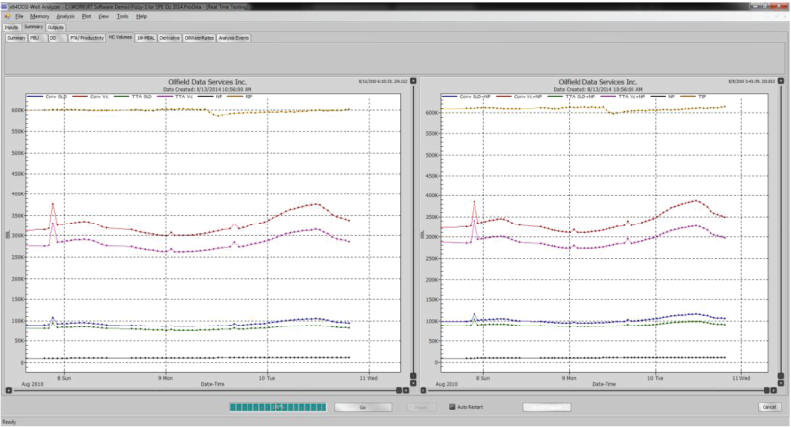
Figure 15 shows the measured WHP and Oil rates, along with the calculated mid-completion BHP. The automatic analysis of the initial drawdown calculated a permeability of 80 md and skin of 4. There are no obvious problems with the completion.
Figure 16 presents the results of the running energy and material balances.
The apparent oil in place out to the oil-water contact was around 600,000 STB (Yellow Line). The minimum recoverable volumes were around 100,000 STB. The hydraulically connected oil varied between 310,000-390,000 STB; the mobile oil varied between 270,000-330,000 STB. This indicated that some of the apparent oil volume was not connected and even more was not mobilized. This difference points to tight streaks in the reservoir and a likely braided stream/channel deposition. This was not a good water-flooding candidate. It should be noted that this was all achieved without having to perform an extended build-up; no revenue/production was “lost” during this evaluation.
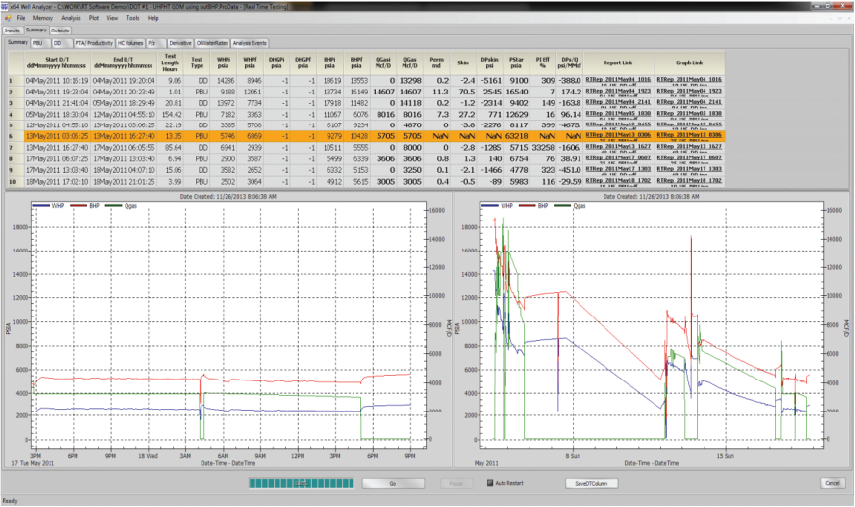
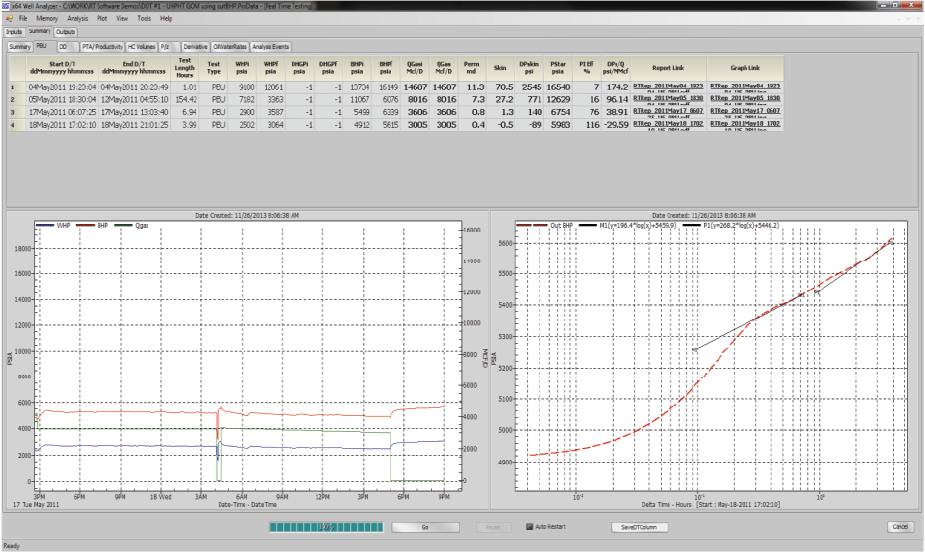
Work Flow for CS #4
The well came on production on July 25, 2010. The drawdown was conducted without significant interruptions and the analysis of moderate permeability and low skin was achieved by the morning of July 26th. Very quickly, the reservoir and production engineers knew that there wasn’t a problem with the completion. After that, it was a bit of a waiting game. It wasn’t until August 7th that the well reached steady-state and the flowing MBAL and EBAL calculations became valid. Once those results became available and the trend continued for a few days, the path forward was fairly obvious.
The basic “issue” with hydrocarbon volume assessments is the “are we there yet?” syndrome. In order for the flowing MBAL/EBAL calculations to work, the well has to be in steady state-flow. This sometimes requires patience and an explanation to management that volume assessments do not happen immediately, unless the reservoir is very, very small.
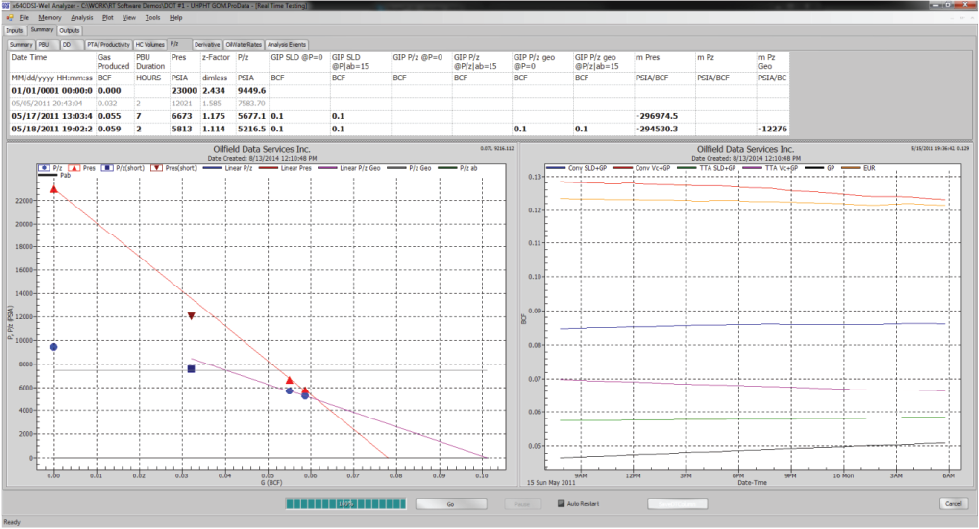
Case Study #5
is from a HP/HT GOM exploration well test that was conducted to determine if there were enough recoverable reserves in a discovery to justify development. Figure 17 presents the WHP, BHP and gas rate during the well test. The data gap between May 7 and May 12 was due to stimulation operations. The large differences between the build-up permeability and the drawdown permeability indicate that the reservoir rock is highly elasto-plastic (high-compressibility a.k.a. squishy rock). Figure 18 shows a summary of the just the build-ups during the test. The build-up analyses also show evidence of extreme rock compaction, coincident with a large drop in reservoir pressure. Figure 19 presents the results of the Static and Flowing Material and Energy Balances. Work Flow for CS #5: This reservoir was tested prior to development because the operator wanted to make sure that developing the field made economic sense. Once the data was gathered and evaluated, the operator chose not to put a $100,000,000 platform on top of $100,000 of gas.
Conclusions
With proper instrumentation, data transfer and storage, with high enough sample frequency and resolution in the data values, it is possible to automate the calculations of some of the more challenging (and tedious) petroleum engineering calculations. This removes many of the bottlenecks and roadblocks in the decision-making process. If continuity holds, continuous rate and mid-completion BHP can be calculated and validated (or red-flagged, if the well is loading). Then ALL of the well tests can be automatically analyzed for skin and permeability without bias, without waiting for the in-house expert to have time to look at it. Productivity and Inverse Productivity can be continually monitored (changes mean something!). Static MBALs and Decline Analysis can also be automated and the apparent reservoir volume can be not only determined (with some variance, of course), but split into its constituent components (gas, oil water, rock compaction).
This shifts the role of a petroleum engineer from looking for information/data to looking at RESULTS, checking them for validity, and thinking about what they mean. It also democratizes these results, so more people in the team can access what the results mean. . .and can decide what to do next. In short, these unbiased automated calculations lead to a more rapid understanding of what is going on in a well/field. This allows a team/company to make decisions (hopefully, the right ones) much more quickly.
Acknowledgements
The authors would like to thank the operators who gave us permission to use their data in this paper. We would also like to thank Calsep for the use of their PVTSim software in the preparation of the data used to generate the Case Studies. The lead author would also like express his deep appreciation to Stacy Newman for the last-minute, late-night review and editing of this submission, as well as Eamonn Montague for his review and corrections of the draft submission to SPE-KL.
References
-
- Bird, R., Stewart, W., Lightfoot, E. Transport Phenomena, John Wiley & Sons, New York, 1960
- Cullender, M.H. and Smith, R.V. (1956), “Practical Solution of Gas-Flow Equations for Wells and Pipelines with Large Temperature Gradients”, Trans., AIME, 207, p281–287.
- Beggs, H. D., and Brill, J.P., “A Study of Two-Phase Flow in Inclined Pipes,” JPT, 607–617, May 1973.
- Hagedorn, A.R., and Brown, K.E., “Experimental Study of Pressure Gradients Occurring During Continuous Two-Phase Flow in Small-Diameter Vertical Conduits,” JPT, April 1965, pp. 475–84.
- Soave, G. (1972). Equilibrium Constants from a Modified Redlich-Kwong Equation of State, Chem. Eng. Sci. 27, 1197–1203.
- Peng, D.Y. and Robinson, D.B. (1976). A New Two-Constant Equation of State, Ind. & Eng. Chem. 15, No.1, 59–64.
- Peneloux A., Rauzy E. and Freze, R (1982). A Consistent Correction for Redlich-Kwong-Soave Volumes. Fluid Phase Equilibria Vol.(8): 7–23.
- Forchheimer, P.: 1901, Wasserbewegung durch Boden, Z. Ver. Deutsch. Ing. 45, 1782–1788.
- Lee, J.: Well Testing, Society of Petroleum Engineers of AIME, Dallas, 1982
- Hurst, W., Unsteady flow of fluids in oil reservoirs, Physics, 5, 20–30, 1934